Pouring system for casting diesel engine block casting
A pouring system, diesel engine technology, applied in casting molding equipment, casting molds, casting mold components, etc., can solve the problems of not easy to fill the molten metal, easy oxidation of molten metal, small metal oxidation, etc., to avoid inclusion defects, reduce surface The effect of oxidation and metal cleaning
- Summary
- Abstract
- Description
- Claims
- Application Information
AI Technical Summary
Problems solved by technology
Method used
Image
Examples
Embodiment Construction
[0019] In order to enable those skilled in the art to better understand the technical solutions of the present invention, the present invention will be further described in detail below in conjunction with specific embodiments.
[0020] see figure 1 , figure 2 , the present invention provides a pouring system for casting diesel engine block castings, which includes a sprue 1, a runner 2, twelve inrunners A3 and twelve inrunners B5, direct pouring The outlet of channel 1 is vertically connected with the inlet of runner 2, and the ingate A3 is arranged symmetrically on both sides of runner 2, the outlet of ingate A3 is connected to the filter device 4, and the filter device 4 is connected to the ingate B5 connected, the height of the gate of the inrunner B 5 is higher than that of the runner 2, and the molten metal flows into the mold 6 of the diesel engine body from the gate of the inrunner B 5 for casting; the cross-sectional area of the sprue 1 is smaller than that of the...
PUM
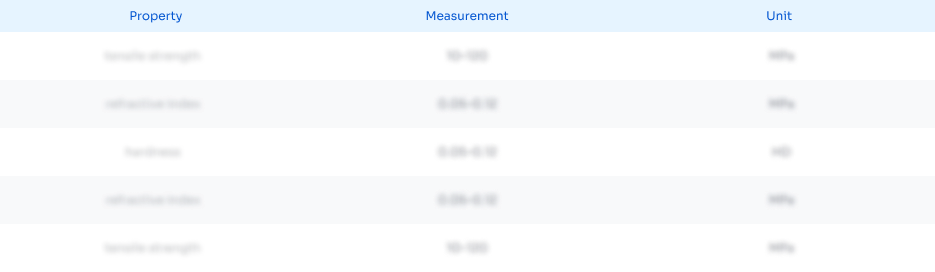
Abstract
Description
Claims
Application Information

- Generate Ideas
- Intellectual Property
- Life Sciences
- Materials
- Tech Scout
- Unparalleled Data Quality
- Higher Quality Content
- 60% Fewer Hallucinations
Browse by: Latest US Patents, China's latest patents, Technical Efficacy Thesaurus, Application Domain, Technology Topic, Popular Technical Reports.
© 2025 PatSnap. All rights reserved.Legal|Privacy policy|Modern Slavery Act Transparency Statement|Sitemap|About US| Contact US: help@patsnap.com