Industrial robot base coordinate measuring method
A technology of industrial robots and base coordinates, which is applied in the direction of measuring devices, instruments, manipulators, etc., can solve problems such as undiscovered robot base coordinates, and achieve good application prospects
- Summary
- Abstract
- Description
- Claims
- Application Information
AI Technical Summary
Problems solved by technology
Method used
Image
Examples
Embodiment Construction
[0020] The preferred embodiments of the present invention will be described in detail below with reference to the accompanying drawings.
[0021] figure 1 It is a test model diagram of the test method of the present invention, and each joint of the whole robot is in the initial mode of zero point. According to the industrial robot technical indicators, the base coordinate system of the robot is located at the contact between the robot base and the bottom surface. Set the robot base coordinate system to O B x B Y B Z B , the coordinate system of the end flange of the robot is O T x T Y T Z T , the measurement coordinate system of the laser tracker is O M x M Y M Z M . Before the robot performance test, it is necessary to accurately find the position of the robot base coordinate system, and calculate the mathematical conversion relationship between the laser tracker test coordinate system and the base coordinate system.
[0022] When the joints of the robot are at ...
PUM
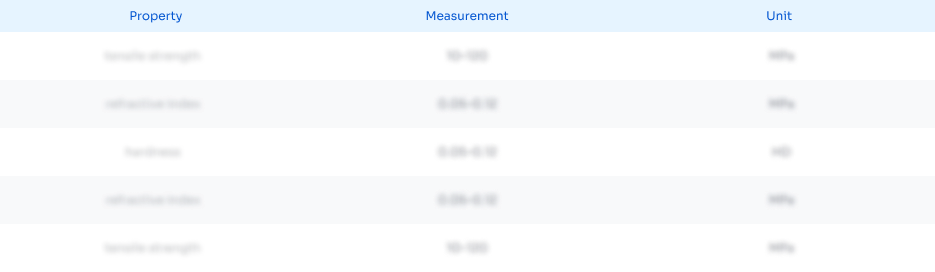
Abstract
Description
Claims
Application Information

- R&D
- Intellectual Property
- Life Sciences
- Materials
- Tech Scout
- Unparalleled Data Quality
- Higher Quality Content
- 60% Fewer Hallucinations
Browse by: Latest US Patents, China's latest patents, Technical Efficacy Thesaurus, Application Domain, Technology Topic, Popular Technical Reports.
© 2025 PatSnap. All rights reserved.Legal|Privacy policy|Modern Slavery Act Transparency Statement|Sitemap|About US| Contact US: help@patsnap.com