Fiber board production method free of sewage discharge
A technology for sewage discharge and production methods, which is applied in the fields of fiber raw materials, fiber raw material treatment, chemical instruments and methods, etc., can solve problems such as substandard discharge and consumption of heat
- Summary
- Abstract
- Description
- Claims
- Application Information
AI Technical Summary
Problems solved by technology
Method used
Examples
Embodiment 1
[0019] An MDF company with an annual output of 80,000 cubic meters in Fujian felt that it was necessary to improve its sewage treatment system after repeatedly receiving fines from the environmental protection department. During the pre-cooking of wood chips, it was changed from direct steam heating to steam heating. The heat sink is heated, and the heat sink heats the wood chip again, thereby increasing the temperature of the wood chip. Then the waste water washed with wood chips is passed through secondary sedimentation, and the small wood slag and bark are first taken away through the mesh belt, and then used as fuel; sediment, gravel and small iron pieces are passed through secondary sedimentation, and then passed through solid-liquid Separator, the iron blocks are collected by magnet adsorption, and under the action of the extruding auger, the water in the material is squeezed out of the mesh screen under the action of the side pressure belt filter, and the sediment is use...
Embodiment 2
[0022] The manufacturer later built a new medium density fiberboard enterprise with an annual output of 250,000 cubic meters. In the design, the sewage treatment equipment and infrastructure needs 5 million were directly saved, and the temperature of the water was raised to 40-60°C during washing, and then The wood chips are transported to the thermal grinder for thermal grinding. Then the waste water washed with wood chips is passed through secondary sedimentation, and the small wood slag and bark are first taken away through the mesh belt, and then used as fuel; sediment, gravel and small iron pieces are passed through secondary sedimentation, and then passed through solid-liquid Separator, the iron blocks are collected by magnet adsorption, and under the action of the extruding auger, the water in the material is squeezed out of the mesh screen under the action of the side pressure belt filter, and the sediment is used as soil for landfill, and the clarified water can be Co...
PUM
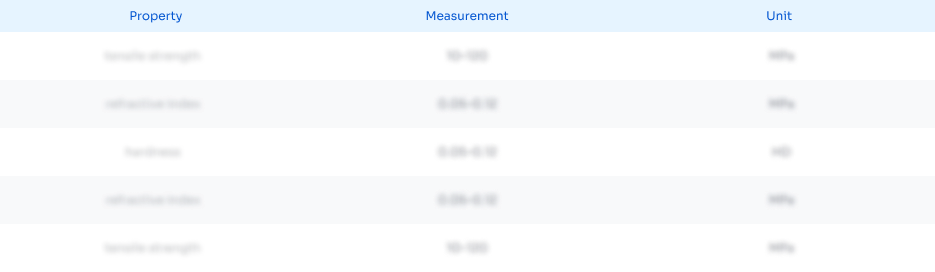
Abstract
Description
Claims
Application Information

- R&D Engineer
- R&D Manager
- IP Professional
- Industry Leading Data Capabilities
- Powerful AI technology
- Patent DNA Extraction
Browse by: Latest US Patents, China's latest patents, Technical Efficacy Thesaurus, Application Domain, Technology Topic, Popular Technical Reports.
© 2024 PatSnap. All rights reserved.Legal|Privacy policy|Modern Slavery Act Transparency Statement|Sitemap|About US| Contact US: help@patsnap.com