Laser cutting machine and energy control system of laser cutting multilayer composite material
A multi-layer composite material and energy control technology, applied in laser welding equipment, manufacturing tools, welding equipment, etc., can solve problems such as discontinuity, traces, control errors, etc., to improve cutting quality, reduce control errors, overcoming the effect of closure
- Summary
- Abstract
- Description
- Claims
- Application Information
AI Technical Summary
Problems solved by technology
Method used
Image
Examples
Embodiment Construction
[0041] The specific embodiments and examples of the present invention will be described in detail below in conjunction with the accompanying drawings. The described specific embodiments are only used to explain the present invention, and are not intended to limit the specific embodiments of the present invention.
[0042] The cutting of multi-layer composite materials has strict and precise requirements on the energy output by the laser. It is necessary to cut through the upper material without damaging the lower material. In fact, the laser cutting control system is used to cut the object according to the pre-designed graphics , to form a laser energy cutting track to realize the cutting of the desired material layer.
[0043] In fact, each metal or non-metal material to be cut has a fixed laser energy that can cut through. The low-power laser on the laser cutting head can be controlled by PWM waves, which involves two control parameters: one is the pulse width. control, usin...
PUM
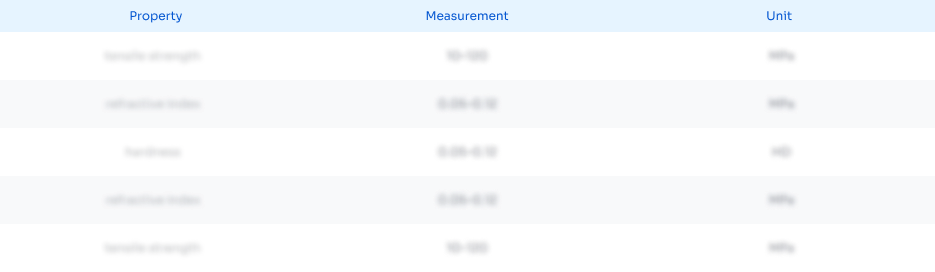
Abstract
Description
Claims
Application Information

- R&D
- Intellectual Property
- Life Sciences
- Materials
- Tech Scout
- Unparalleled Data Quality
- Higher Quality Content
- 60% Fewer Hallucinations
Browse by: Latest US Patents, China's latest patents, Technical Efficacy Thesaurus, Application Domain, Technology Topic, Popular Technical Reports.
© 2025 PatSnap. All rights reserved.Legal|Privacy policy|Modern Slavery Act Transparency Statement|Sitemap|About US| Contact US: help@patsnap.com