Quenching process applied to high-hardness engineering machinery
A technology of engineering machinery and high hardness, which is applied in the direction of quenching devices, manufacturing tools, metal processing equipment, etc., can solve the problems of bucket tooth casting, troublesome operation, etc., and achieve the goals of improving service life, convenient application of release fluid, and improving efficiency Effect
- Summary
- Abstract
- Description
- Claims
- Application Information
AI Technical Summary
Problems solved by technology
Method used
Image
Examples
Embodiment
[0028] A quenching process applied to high-hardness construction machinery for making bucket teeth, specifically through the following steps:
[0029] a. Sand box device: the sand box device includes a push rod 3, a rotatable upper sand box 11 and a centrifugally rotatable lower sand box 12, and the upper sand box 11 is provided with a sprue 13 and a demoulding mechanism 14. The lower sand box 12 is provided with a bucket tooth cavity 15, and an electric heating tube 1 is arranged around the bucket tooth cavity 15; the upper sand box 11 is rotated so that the sprue 13 or the demoulding mechanism 14 and The bucket tooth cavity 15 of the lower flask 12 is mated and connected; the ejector rod 3 traverses through the lower flask 12 to the inside of the bucket tooth cavity 15, and is used for casting a connecting hole for clamping the bucket tooth pin ( figure 1 ).
[0030] The demoulding mechanism 14 includes a push rod 3, a liquid inlet channel 16 and a box 17 for storing the de...
PUM
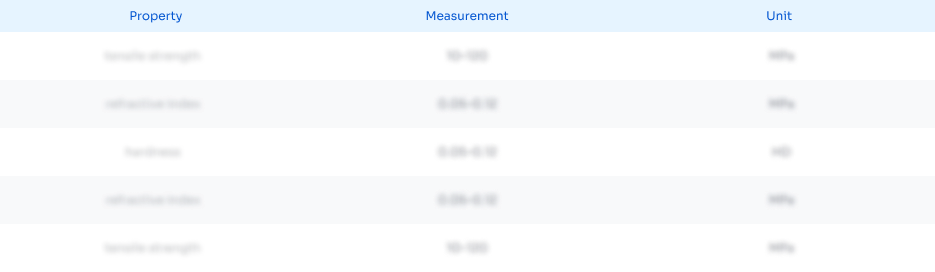
Abstract
Description
Claims
Application Information

- R&D
- Intellectual Property
- Life Sciences
- Materials
- Tech Scout
- Unparalleled Data Quality
- Higher Quality Content
- 60% Fewer Hallucinations
Browse by: Latest US Patents, China's latest patents, Technical Efficacy Thesaurus, Application Domain, Technology Topic, Popular Technical Reports.
© 2025 PatSnap. All rights reserved.Legal|Privacy policy|Modern Slavery Act Transparency Statement|Sitemap|About US| Contact US: help@patsnap.com