Multi-color strip double-color insulated cable core and its manufacturing mold and manufacturing method
A technology for making insulated cables and molds, which is applied in the direction of insulated cables, cable/conductor manufacturing, and insulated conductors. It can solve problems such as narrow color line width, gap in core insulation technology, and difficult identification of cores.
- Summary
- Abstract
- Description
- Claims
- Application Information
AI Technical Summary
Problems solved by technology
Method used
Image
Examples
Embodiment Construction
[0033] The following is attached Figure 1 to Figure 10 The given examples further illustrate the manufacturing method of the multi-color striped double-color insulated cable core of the present invention. The manufacturing method of the multi-color striped double-color insulated cable core of the present invention is not limited to the description of the following embodiments.
[0034] see Figure 5 to Figure 7 The mold cover MX of the multi-color strip and double-color insulated cable core of the present invention includes a cylindrical contour surface 10, end faces 40 and outer end surfaces 70 at both ends, and a cylindrical extrusion hole 20 and an extrusion hole 20 are arranged in the mold sleeve MX. The conical forming hole 30 formed by the coaxial butt joint of the packing hole 20, one end of the extrusion hole 20 is coaxially connected with the small end of the forming hole 30, the other end of the extrusion hole 20 intersects with the outer end surface 70, and the la...
PUM
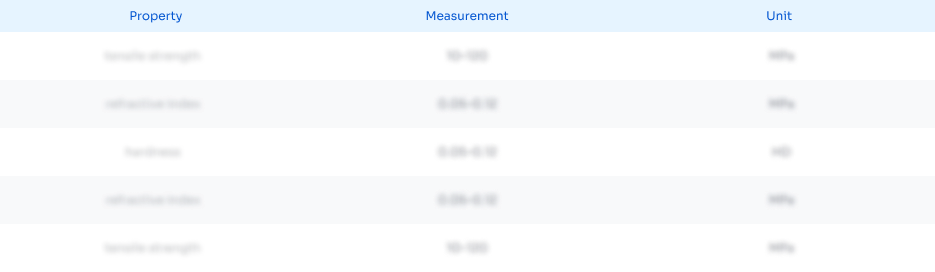
Abstract
Description
Claims
Application Information

- R&D Engineer
- R&D Manager
- IP Professional
- Industry Leading Data Capabilities
- Powerful AI technology
- Patent DNA Extraction
Browse by: Latest US Patents, China's latest patents, Technical Efficacy Thesaurus, Application Domain, Technology Topic, Popular Technical Reports.
© 2024 PatSnap. All rights reserved.Legal|Privacy policy|Modern Slavery Act Transparency Statement|Sitemap|About US| Contact US: help@patsnap.com