Singly dyed yarn production process
A production process and yarn dyeing technology, applied to spinning machines, continuous winding spinning machines, deburring devices, etc., can solve the problem of insufficient carding, uneven slubs, and failure to effectively guarantee product quality and reliability and other problems, to achieve the effect of fully combing and low cost
- Summary
- Abstract
- Description
- Claims
- Application Information
AI Technical Summary
Problems solved by technology
Method used
Examples
Embodiment
[0020] The production technology of single-dyed yarn comprises the steps:
[0021] 1) Raw material control: use raw cotton with good slenderness and uniformity, low short-lint rate, and few defects, and use 1.33 dtex*38 mm superior high-strength cotton polyester fiber for knitting polyester;
[0022] 2) Process flow:
[0023] a: Carding: adopt the process principle of light weight, strong carding and low speed;
[0024] b: Drawing head: 6 pieces are combined, and a small draft design is adopted to design a small draft, and the unevenness caused by the draft is reduced.
[0025] c: Two parallels and three parallels: two parallels and three parallels use 8 parallels to ensure that the pressure of the cradle is consistent at both ends, and use large-diameter top rollers;
[0026] d: Roving: Adopt JWF1415 four-roller roving frame with servo motor frequency conversion adjustment function, which can reduce the details of switch machine and accidental drafting, ensure the consisten...
PUM
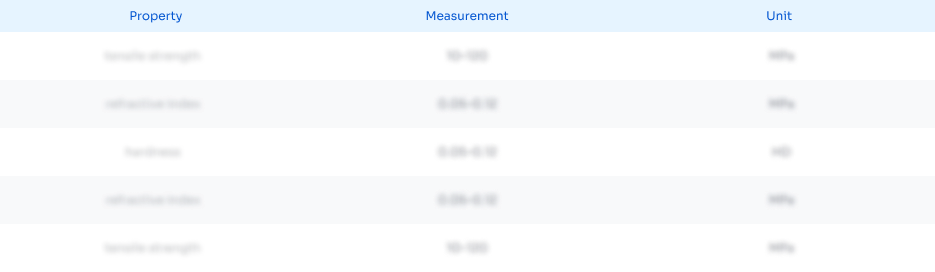
Abstract
Description
Claims
Application Information

- R&D
- Intellectual Property
- Life Sciences
- Materials
- Tech Scout
- Unparalleled Data Quality
- Higher Quality Content
- 60% Fewer Hallucinations
Browse by: Latest US Patents, China's latest patents, Technical Efficacy Thesaurus, Application Domain, Technology Topic, Popular Technical Reports.
© 2025 PatSnap. All rights reserved.Legal|Privacy policy|Modern Slavery Act Transparency Statement|Sitemap|About US| Contact US: help@patsnap.com