Preparation process of alloy mold core for high-temperature alloy single crystal blade precision casting
A single crystal blade and preparation process technology, applied in other manufacturing equipment/tools, mechanical equipment, turbines, etc., can solve the problems of low yield, high scrap rate of alloy mold cores, and increased production cost of hollow-core turbine blades. High qualified rate of finished products, small deformation, small high temperature deformation effect
- Summary
- Abstract
- Description
- Claims
- Application Information
AI Technical Summary
Problems solved by technology
Method used
Image
Examples
Embodiment 1-3
[0042] The formula of embodiment 1-3 metal powder and non-metallic powder is shown in Table 1
[0043]
[0044] According to the above formula, put the metal powder and non-metal powder in a dry mixer and stir them thoroughly for 1 hour, and dry them in a dryer for 3 hours;
[0045] Then, put the fully dried and stirred powder into the acetone solution, and wet mix for 4 hours;
[0046] Next, place the wet-mixed raw materials in an oven and heat to remove the acetone solvent. After the acetone solvent is removed, place the raw materials after the solvent removal in a hopper and heat until the temperature of the raw materials is 130° C.;
[0047] Next, feed the raw material at 130°C into the mold with the heating device through the feeding device;
[0048] Then, start the press, press molding;
[0049] Next, take the formed workpiece out of the mold, because the workpiece has a certain temperature, it can be cut and processed, and then put the mold blank into the CNC equip...
PUM
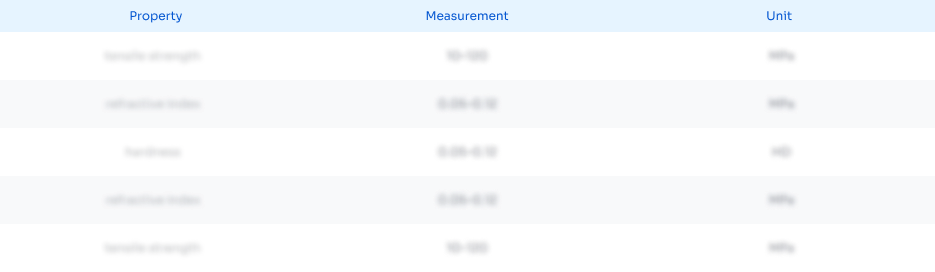
Abstract
Description
Claims
Application Information

- R&D
- Intellectual Property
- Life Sciences
- Materials
- Tech Scout
- Unparalleled Data Quality
- Higher Quality Content
- 60% Fewer Hallucinations
Browse by: Latest US Patents, China's latest patents, Technical Efficacy Thesaurus, Application Domain, Technology Topic, Popular Technical Reports.
© 2025 PatSnap. All rights reserved.Legal|Privacy policy|Modern Slavery Act Transparency Statement|Sitemap|About US| Contact US: help@patsnap.com