Method and system for dynamic water volume control in cooling zone of continuous casting machine
A technology of water quantity control and cooling zone, applied in the field of continuous casting, can solve the problems of affecting the water quantity in the cooling zone, the effect of slab cooling, and the effect of not considering the pulling speed, etc.
- Summary
- Abstract
- Description
- Claims
- Application Information
AI Technical Summary
Problems solved by technology
Method used
Image
Examples
Embodiment 1
[0112] This embodiment takes the cooling water control of the secondary cooling zone in the continuous casting process as an example. A continuous casting machine has 12 cooling zones. The implementation steps of this embodiment are the same in each cooling zone. Therefore, only cooling Zone 4 will be detailed and calculated, and the specific steps are as follows:
[0113] 1) Initialize the cooling weight coefficient Coeff of the cooling zone i i ,and n is a positive integer, 1 is the serial number of the crystallizer cooling zone, 2~n is the serial number of the secondary cooling zone, and the cooling weight coefficient of cooling zone i is shown in Table 1:
[0114] cooling zonei
1
2
3
4
5
6
7
8
9
10
11
12
Coeff i
0.1
0.09
0.11
0.14
0.12
0.09
0.06
0.09
0.07
0.06
0.03
0.04
[0115] Table 1
[0116] 2) Record the moment when slice j enters and leaves cooling zone i and and th...
PUM
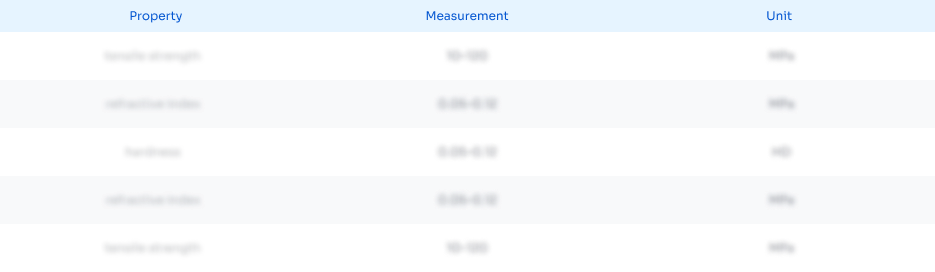
Abstract
Description
Claims
Application Information

- R&D
- Intellectual Property
- Life Sciences
- Materials
- Tech Scout
- Unparalleled Data Quality
- Higher Quality Content
- 60% Fewer Hallucinations
Browse by: Latest US Patents, China's latest patents, Technical Efficacy Thesaurus, Application Domain, Technology Topic, Popular Technical Reports.
© 2025 PatSnap. All rights reserved.Legal|Privacy policy|Modern Slavery Act Transparency Statement|Sitemap|About US| Contact US: help@patsnap.com