Method for synthesis of sodalite from kaolinite
A technology of kaolinite and sodalite, which is applied in the direction of aluminum silicate and silicate, can solve the problems of high production cost, complex sodalite synthesis process, and low purity of synthetic sodalite, and achieve low cost, Significant environmental and economic benefits, and the effect of improving the utilization rate of strong alkali
- Summary
- Abstract
- Description
- Claims
- Application Information
AI Technical Summary
Problems solved by technology
Method used
Image
Examples
Embodiment 1
[0026] Calcinate kaolinite in a box-type resistance furnace at 750°C for 2 hours to obtain a metakaolinite sample, weigh 5g of metakaolinite each time and place it in a reactor with a stirring device, and mix the prepared 10mol / L The sodium hydroxide solution is added into the reactor while stirring, the solid-liquid ratio is 1:10 (g / ml or kg / L), heated from room temperature to 95°C, and reacted for 8 hours under this condition, and the product synthesized by the reaction is carried out Centrifuge or filter, wash until the pH is 9, and dry at 100°C to obtain the desired product. After recovering the obtained filtrate and washing water, sodium hydroxide caustic soda is added to form a solution of corresponding concentration, which can be recycled.
[0027] figure 1 It is the XRD pattern of the product synthesized in this embodiment, as can be seen from the figure, the peaks appearing at 13.9, 24.3, 31.5, 34.5, 42.6 correspond to the standard cards of sodalite one by one, and i...
Embodiment 2
[0030] Calcinate kaolinite in a box-type resistance furnace at 750°C for 2 hours to obtain a metakaolinite sample. Weigh 5g of metakaolinite each time and place it in a reactor with a stirring device. The prepared 25mol / L The sodium hydroxide solution is added into the reactor while stirring, the solid-to-liquid ratio is 1:2, heated from room temperature to 85°C, and reacted for 8 minutes under this condition, and the product synthesized by the reaction is centrifuged or filtered and washed until the pH is 9. The desired product can be obtained after drying at 100°C.
Embodiment 3
[0032] Calcinate kaolinite in a box-type resistance furnace at 750°C for 2 hours to obtain a metakaolinite sample, weigh 5g of metakaolinite each time and place it in a reactor with a stirring device, and mix the prepared 10mol / L Add sodium hydroxide solution to the reactor while stirring, the solid-to-liquid ratio is 1:10, react at room temperature (25°C) for 120h, centrifuge or filter and wash the product synthesized by the reaction until the pH is 9, after The desired product was obtained after drying at 100°C.
PUM
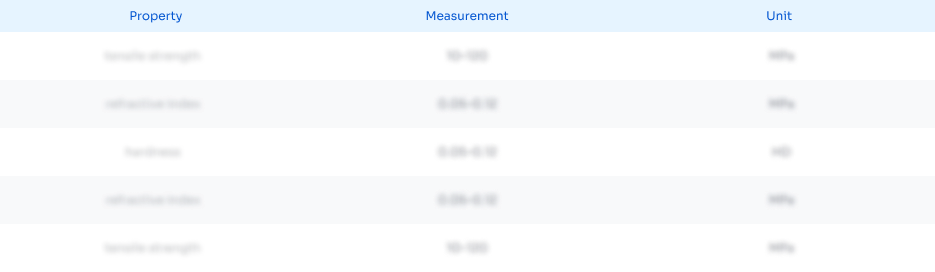
Abstract
Description
Claims
Application Information

- R&D
- Intellectual Property
- Life Sciences
- Materials
- Tech Scout
- Unparalleled Data Quality
- Higher Quality Content
- 60% Fewer Hallucinations
Browse by: Latest US Patents, China's latest patents, Technical Efficacy Thesaurus, Application Domain, Technology Topic, Popular Technical Reports.
© 2025 PatSnap. All rights reserved.Legal|Privacy policy|Modern Slavery Act Transparency Statement|Sitemap|About US| Contact US: help@patsnap.com