Co-curing molding process for double-sided reinforced fuselage frame of composite materials
A technology of curing molding and process method, which is applied in the field of composite material manufacturing, can solve the problems of increased manufacturing risk, long manufacturing cycle, and high production cost, and achieve the effects of improving economy and safety, low cost, and excellent product quality
- Summary
- Abstract
- Description
- Claims
- Application Information
AI Technical Summary
Problems solved by technology
Method used
Image
Examples
Embodiment Construction
[0040] In the following detailed description of the preferred embodiments, reference will be made to the accompanying drawings which form a part hereof. The accompanying drawings show, by way of example, specific embodiments in which the invention can be practiced. The illustrated embodiments are not intended to be exhaustive of all embodiments in accordance with the invention. It is to be understood that other embodiments may be utilized and structural or logical modifications may be made without departing from the scope of the present invention.
[0041] like Figure 1a , 1b As shown in and 1c, the present invention takes the molding of a composite material double-sided reinforced fuselage frame structure as an example, the fuselage frame includes a laminate 3, and three longitudinal T-shaped ribs 1 are installed on the first side of the laminate 3. , two transverse T-shaped ribs 2 are installed on the second side, and the process is as follows:
[0042] (1) Manufacture o...
PUM
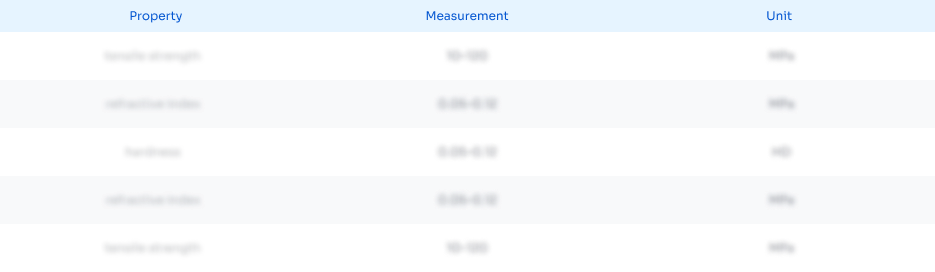
Abstract
Description
Claims
Application Information

- Generate Ideas
- Intellectual Property
- Life Sciences
- Materials
- Tech Scout
- Unparalleled Data Quality
- Higher Quality Content
- 60% Fewer Hallucinations
Browse by: Latest US Patents, China's latest patents, Technical Efficacy Thesaurus, Application Domain, Technology Topic, Popular Technical Reports.
© 2025 PatSnap. All rights reserved.Legal|Privacy policy|Modern Slavery Act Transparency Statement|Sitemap|About US| Contact US: help@patsnap.com