Ultrasonic motor with high rotation precision structure and stator and rotor preloading method
A technology of rotation precision and ultrasonic motor, which is applied in the manufacture of stator/rotor body, piezoelectric effect/electrostrictive or magnetostrictive motor, generator/motor, etc. Coaxiality is difficult to meet high coaxial requirements, etc., to achieve the effect of improved rotation accuracy, high rotation accuracy, and improved assembly accuracy
- Summary
- Abstract
- Description
- Claims
- Application Information
AI Technical Summary
Problems solved by technology
Method used
Image
Examples
specific Embodiment approach 1
[0012] Specific implementation mode one: combine Figure 1-Figure 3 Explain that an ultrasonic motor with a high rotation precision structure in this embodiment includes an upper cover 10, a base 5, a rotor shaft 1, a stator 6, a rotor 8, a rotor flange 20, rotor screws 17 and two angular contact ball bearings 4;
[0013] The upper cover 10 and the base 5 are respectively processed with coaxial through holes with the same inner diameter, and an angular contact ball bearing 4 is installed in each of the two coaxial through holes, and the angular contact lines of the two angular contact ball bearings 4 are in the same direction and parallel Arrangement, the rotor shaft 1 is installed on two angular contact ball bearings 4, the stator 6 is installed on the base 5, the rotor 8 and the stator 6 are arranged between the two angular contact ball bearings 4, the rotor flange 20 is arranged on the angular contact ball Between the bearing 4 and the rotor 8, the rotor flange 20 is firml...
specific Embodiment approach 2
[0015] Specific implementation mode two: combination figure 1 and figure 2 Explain that an ultrasonic motor with a high rotation precision structure in this embodiment also includes a preload nut 2 and a washer 3; a preload nut 2 is screwed on the rotor shaft 1 adjacent to the base 5, and the preload nut 2 is in contact with the corner Washers 3 are arranged between the ball bearings 4 . With such a design, the high rotation accuracy and precise preload of the ultrasonic motor can be realized, which meets the design requirements and actual needs. Others are the same as in the first embodiment.
specific Embodiment approach 3
[0016] Specific implementation mode three: combination figure 1 and figure 2 Explain that an ultrasonic motor with a high rotation precision structure in this embodiment also includes a pressure ring 11, a gasket 15, a bearing preload adjustment ring 16 and a pressure ring screw 19; the pressure ring 11 is installed on the upper cover 10 through the pressure ring screw 19 Above, between the pressure ring 11 and the angular contact ball bearing 4 there is a bearing preload adjusting ring 16 which is in contact with the outer ring of the angular contact ball bearing 4, and between the rotor flange 20 and the angular contact ball bearing 4 there is a contact The inner ring of the ball bearing 4 contacts the gasket 15 . With such a design, the high rotation accuracy and precise preload of the ultrasonic motor can be realized, which meets the design requirements and actual needs. Others are the same as in the first or second embodiment.
PUM
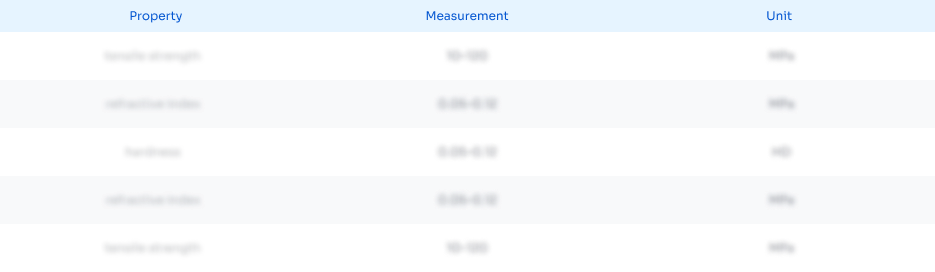
Abstract
Description
Claims
Application Information

- R&D Engineer
- R&D Manager
- IP Professional
- Industry Leading Data Capabilities
- Powerful AI technology
- Patent DNA Extraction
Browse by: Latest US Patents, China's latest patents, Technical Efficacy Thesaurus, Application Domain, Technology Topic, Popular Technical Reports.
© 2024 PatSnap. All rights reserved.Legal|Privacy policy|Modern Slavery Act Transparency Statement|Sitemap|About US| Contact US: help@patsnap.com