A kind of silt-free sintering brick manufacturing process
A production process and sinter-free technology, which is applied in the field of building bricks, can solve problems such as insufficient performance and cost waste, and achieve the effects of avoiding performance conflicts, avoiding interactions, and improving utilization
- Summary
- Abstract
- Description
- Claims
- Application Information
AI Technical Summary
Problems solved by technology
Method used
Examples
Embodiment 1
[0021] Step 1, preparing and extracting sludge, removing garbage, adjusting the particle size of the sludge, and then adjusting the moisture content, so that the moisture content of the adjusted sludge is 60%;
[0022] Step 2, adding quicklime to the sludge obtained after the treatment in step 1, the quicklime and sludge are added in a ratio of 1:10 by mass, fully stirred, and then left to stand for 2 days;
[0023] Step 3: Add additives, stones, sand, and cement to the silt after standing, wherein the additives are calcium chloride 38%, sodium chloride 16%, magnesium chloride 3%, potassium chloride 2%, ferrous iron 4% by mass fraction % aqueous solution proportioning is made, and silt, additive, stone, sand, cement are counted as silt 65,2%, additive 0.8%, stone 12%, sand 10%, cement 12% and fully stir by mass fraction, obtain mixed materials;
[0024] Step 4: Extrude the mixed materials to make adobes, and then dry them for 18 hours to form silt-free bricks.
[0025] The n...
Embodiment 2
[0027] Step 1, preparing and extracting sludge, removing garbage, adjusting the particle size of the sludge, and then adjusting the moisture content, so that the moisture content of the adjusted sludge is 65%;
[0028] Step 2, adding quicklime to the sludge obtained after the treatment in step 1, the quicklime and the sludge are added in a ratio of 1:8 by mass, fully stirred, and then left to stand for 5 days;
[0029] Step 3: Add additives, stones, sand, and cement to the silt after standing, wherein the additives are calcium chloride 38%, sodium chloride 16%, magnesium chloride 3%, potassium chloride 2%, ferrous iron 4% by mass fraction % aqueous solution ratio is made, and the silt, additives, stones, sand, and cement are calculated as 70% of silt, 0.5% of additives, 9% of stones, 10.5% of sand, and 10% of cement by mass fraction and fully stirred to obtain a mixed material ;
[0030] Step 4: Extrude the mixed materials to make adobes, and then dry them for 20 hours to for...
Embodiment 3
[0032] Step 1, preparing and extracting sludge, removing garbage, adjusting the particle size of the sludge, and then adjusting the moisture content, so that the moisture content of the adjusted sludge is 70%;
[0033] Step 2, adding quicklime to the sludge obtained after the treatment in step 1, the quicklime and sludge are added in a mass ratio of 1:6.5, fully stirred, and then left to stand for 7 days;
[0034] Step 3: Add additives, stones, sand, and cement to the silt after standing, wherein the additives are calcium chloride 38%, sodium chloride 16%, magnesium chloride 3%, potassium chloride 2%, ferrous iron 4% by mass fraction % aqueous solution ratio is made, and silt, additives, stones, sand, and cement are calculated as 75% of silt, 0.5% of additives, 8.5% of stones, 8% of sand, and 8% of cement by mass fraction and fully stirred to obtain a mixed material ;
[0035] Step 4: Extrude the mixed materials to make adobes, and then dry them for 24 hours to form silt-free...
PUM
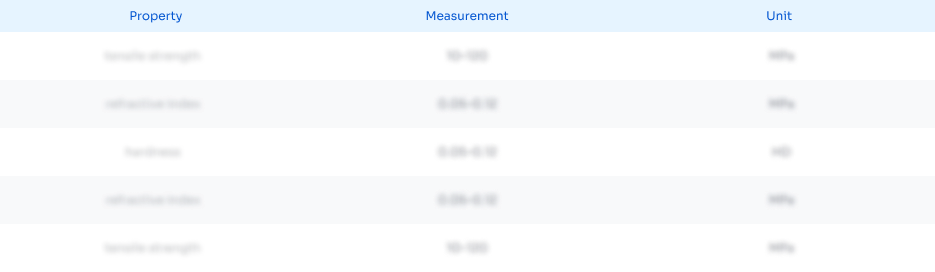
Abstract
Description
Claims
Application Information

- R&D
- Intellectual Property
- Life Sciences
- Materials
- Tech Scout
- Unparalleled Data Quality
- Higher Quality Content
- 60% Fewer Hallucinations
Browse by: Latest US Patents, China's latest patents, Technical Efficacy Thesaurus, Application Domain, Technology Topic, Popular Technical Reports.
© 2025 PatSnap. All rights reserved.Legal|Privacy policy|Modern Slavery Act Transparency Statement|Sitemap|About US| Contact US: help@patsnap.com