High strength and flame retardant cable insulation sheath material and preparation method thereof
A cable insulation and sheathing material technology, applied in insulators, rubber insulators, organic insulators, etc., can solve the problems of endangering life and property safety, unreasonable mix of ingredients, general insulation performance, etc., achieving easy operation, excellent aging resistance, The effect of short burning distance
- Summary
- Abstract
- Description
- Claims
- Application Information
AI Technical Summary
Problems solved by technology
Method used
Examples
preparation example Construction
[0024] A preparation method of a high-strength flame-resistant cable insulation sheath material, comprising the steps of:
[0025] S1. Weigh a certain amount of 22-35 parts of PVC polyvinyl chloride, 15-25 parts of polyether ether ketone resin, 16-22 parts of trioctyl trimellitate, 10-15 parts of nano-bauxite, and 15 parts of silicon micropowder. -22 parts, ethylene propylene rubber 10-20 parts, copper sulfate 11-15 parts, liquid wax 33-36 parts, carbon fiber 10-20 parts, aluminum naphthenate 3-9 parts, stabilizer 6-10 parts Thoroughly mix and stir in a mixing mixer for 5-10 minutes to obtain a mixture;
[0026] S2. Add 2-6 parts of anti-aging agent, 5-8 parts of flame retardant and 2-6 parts of plasticizer to the mixture obtained in step S1, first react at a temperature of 60-80°C for 15-20min, and then use 500- Stir rapidly at a rate of 800r / min for 20-30min, then pour into a single-screw granulator for granulation;
[0027] S3. After cooling the product obtained in step S...
Embodiment 1
[0031] S1. Weigh a certain amount of 22 parts of PVC polyvinyl chloride, 15 parts of polyether ether ketone resin, 16 parts of trioctyl trimellitate, 10 parts of nano-bauxite, 15 parts of silicon micropowder, 10 parts of ethylene-propylene rubber, 11 parts of copper sulfate, 33 parts of liquid wax, 10 parts of carbon fiber, 3 parts of aluminum naphthenate, and 6 parts of stabilizer were added to a high-efficiency mixing mixer and fully mixed and stirred for 5 minutes to obtain a mixture;
[0032] S2. Add 2 parts of anti-aging agent, 5 parts of flame retardant and 2 parts of plasticizer to the mixture obtained in step S1, first react at a temperature of 60°C for 15 minutes, then stir rapidly at a rate of 500r / min for 20 minutes, and then pour Single-screw granulator granulation;
[0033] S3. After cooling the product obtained in step S2, the cable insulation sheath material is obtained.
Embodiment 2
[0035] S1. Weigh a certain amount of 27 parts of PVC polyvinyl chloride, 22 parts of polyether ether ketone resin, 18 parts of trioctyl trimellitate, 12 parts of nano-bauxite, 18 parts of silicon micropowder, 15 parts of ethylene-propylene rubber, 13 parts of copper sulfate, 34 parts of liquid wax, 16 parts of carbon fiber, 5 parts of aluminum naphthenate, and 7 parts of stabilizer are added to a high-efficiency mixing mixer and fully mixed and stirred for 5-10 minutes to obtain a mixture;
[0036] S2. Add 4 parts of anti-aging agent, 6 parts of flame retardant and 4 parts of plasticizer to the mixture obtained in step S1, first react at a temperature of 60-80°C for 15-20min, and then rapidly at a rate of 500-800r / min Stir for 20-30min, then pour into single-screw granulator for granulation;
[0037] S3. After cooling the product obtained in step S2, the cable insulation sheath material is obtained.
PUM
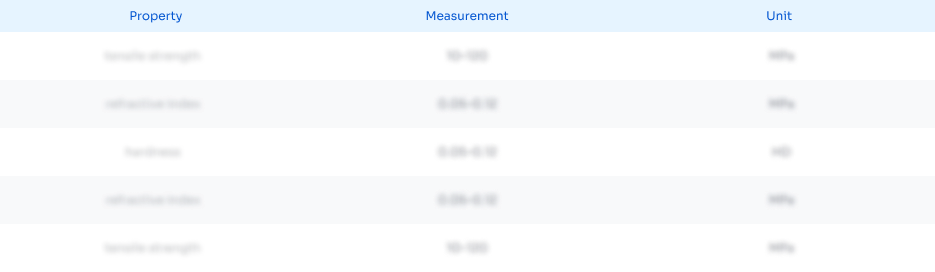
Abstract
Description
Claims
Application Information

- R&D
- Intellectual Property
- Life Sciences
- Materials
- Tech Scout
- Unparalleled Data Quality
- Higher Quality Content
- 60% Fewer Hallucinations
Browse by: Latest US Patents, China's latest patents, Technical Efficacy Thesaurus, Application Domain, Technology Topic, Popular Technical Reports.
© 2025 PatSnap. All rights reserved.Legal|Privacy policy|Modern Slavery Act Transparency Statement|Sitemap|About US| Contact US: help@patsnap.com