Drying equipment and drying process applied to thermal dye sublimation body paper
A drying equipment and thermal sublimation technology, applied in the dryer section, papermaking, papermaking and other directions, can solve the problems of hair loss and powder loss, affecting the printing effect, affecting the product quality, etc., to reduce the expansion ratio, small deformation, and improve smoothness degree of effect
- Summary
- Abstract
- Description
- Claims
- Application Information
AI Technical Summary
Problems solved by technology
Method used
Image
Examples
Embodiment Construction
[0030] Such as figure 1 As shown, a kind of drying equipment applied to sublimation base paper includes a first frame body, a second frame body and a third frame body (the first frame body, the second frame body and the third frame body in the figure are all shown), wherein the first frame body is provided with a large drying cylinder 11, and the front and bottom of the large drying cylinder 11 are provided with several idler rollers 12 (the direction of travel of the paper 7 is the rear, the same below), As a specific implementation, in this embodiment, two supporting rollers 12 are provided. The main function of setting the supporting rollers 12 is to make the surface of the paper 7 smoother through the extrusion between the supporting rollers 12 and the large drying cylinder 11. . like this figure 1 As shown, the large drying cylinder 11 forms a pre-drying of the paper 7. The main purpose of setting a pre-drying is to add a pre-drying before the primary drying process, ...
PUM
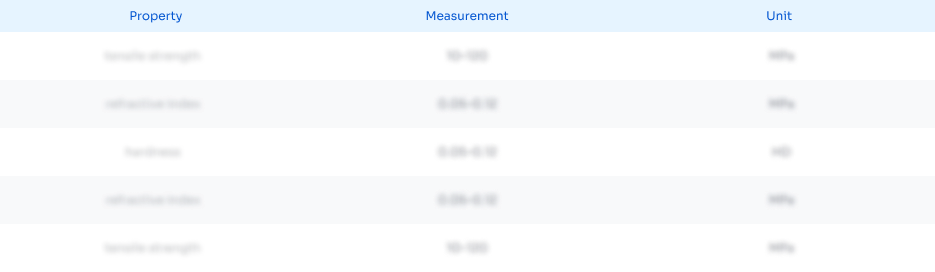
Abstract
Description
Claims
Application Information

- R&D
- Intellectual Property
- Life Sciences
- Materials
- Tech Scout
- Unparalleled Data Quality
- Higher Quality Content
- 60% Fewer Hallucinations
Browse by: Latest US Patents, China's latest patents, Technical Efficacy Thesaurus, Application Domain, Technology Topic, Popular Technical Reports.
© 2025 PatSnap. All rights reserved.Legal|Privacy policy|Modern Slavery Act Transparency Statement|Sitemap|About US| Contact US: help@patsnap.com