In-situ test system and method for mechanical properties of nano material
A technology of nanomaterials and in-situ testing, applied in the direction of scanning probe technology, instruments, etc., can solve the problems that samples cannot be manipulated and measured at the same time, it is difficult to achieve reliable fixation, microscopic observation with external field effect, etc., to achieve convenient real-time observation, Reliable fixation, small size effect
- Summary
- Abstract
- Description
- Claims
- Application Information
AI Technical Summary
Problems solved by technology
Method used
Image
Examples
example 1
[0085] Example 1: Application of the joint testing system of the present invention in in-situ three-dimensional topography imaging
[0086] The principle of three-dimensional topography imaging using this joint test system is the same as that of commercial AFM imaging. In the experiment, the probe 281 is the NSC11 probe of μmasch company, and its elastic constant is 3.0N / m. The standard AFM grating sample is selected as the sample, and its calibration size is 2 μm in cycle width and 200 nm in calibration height. Selecting this standard sample can realize the three-dimensional shape imaging function, and can also calibrate the displacement accuracy of the test system. Install the sample and probe 281 according to step 1.2 and step 1.3 respectively, and the topography of the obtained standard sample is shown in Figure 6 shown. The experimental research found that the period width measured by scanning the picture of the standard grating sample is 2.1±0.1μm, and the grid height...
example 2
[0087] Example 2: Application of the joint testing system of the present invention in the process of manipulating nanomaterials in situ
[0088] Different from the AFM scanning imaging mode, the manipulation and testing functions of the scanning probe testing unit 2 are realized by closing the Z-axis piezoelectric ceramic 233 feedback. In the imaging mode, the probe 281 is in contact with the sample, and the expansion and contraction of the Z-axis piezoelectric ceramic 233 is adjusted in real time through signal feedback, so that the probe 281 and the sample always maintain a certain relative height to maintain a certain physical quantity related to the distance between the needle tip and the sample. . In the manipulation and test mode, the feedback of the displacement of the Z-axis piezoelectric ceramic 233 is turned off, so that when the needle tip moves, it can directly collide with the sample to generate an interaction force.
[0089] Taking the planar movement arrangement ...
example 3
[0090] Example 3: Application of the combined testing system of the present invention in the in-situ three-point bending test of silver nanowires
[0091] Dilute the silver nanowires with uniform thickness and typical five-twin structure with alcohol solution and ultrasonically oscillate to disperse them evenly, then drop them onto the silicon wafer with etched microgrooves with a dropper, and wait for the alcohol to After the solution volatilizes, part of the nanowires are suspended across the two ends of the etching groove, and the contact parts are bonded together by adhesion, such as Figure 4 shown. The probe 281 selected for the in-situ three-point bending test is a commercial μmasch probe, the elastic constants are 3.5 N / m (NSC18), and the radius of curvature of the tip is 10 nm. Install the prepared sample and probe 281 according to steps 1.2 and 1.3 respectively, and perform an in-situ three-point bending test.
[0092] The study found that for silver nanowires with...
PUM
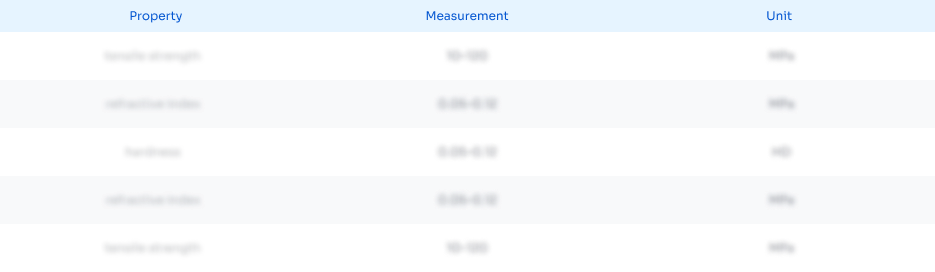
Abstract
Description
Claims
Application Information

- Generate Ideas
- Intellectual Property
- Life Sciences
- Materials
- Tech Scout
- Unparalleled Data Quality
- Higher Quality Content
- 60% Fewer Hallucinations
Browse by: Latest US Patents, China's latest patents, Technical Efficacy Thesaurus, Application Domain, Technology Topic, Popular Technical Reports.
© 2025 PatSnap. All rights reserved.Legal|Privacy policy|Modern Slavery Act Transparency Statement|Sitemap|About US| Contact US: help@patsnap.com