Low-salt recycling technology for mechanical cutting emulsified liquid waste
A technology of mechanical cutting and waste liquid, applied in chemical instruments and methods, special compound water treatment, oxidized water/sewage treatment, etc., can solve the problems of low electrochemical separation efficiency, affecting the recycling route, and low wastewater recycling rate. , to achieve the effect of reducing the dosage, reducing the treatment cost and saving the cost of water
- Summary
- Abstract
- Description
- Claims
- Application Information
AI Technical Summary
Problems solved by technology
Method used
Image
Examples
Embodiment 1
[0048] The emulsified waste liquid comes from the lubricating liquid and cleaning liquid produced by an engine manufacturing plant in Shanghai. Use 0.4% NaOH solution to adjust the pH to 5. The waste water begins to evaporate into water vapor at a negative pressure (80kPa) and a temperature of 70°C. The water vapor is condensed into a distilled clear liquid, which is collected and discharged into the multi-stage combined advanced oxidation reactor 03; Add manganese dioxide (as an ozone catalyst) in the reactor, the dosage is 100mg / L, the dosage of ozone is 1mg / L, the concentration of ozone is 60mg / L, and the hydraulic retention time is 30min; 2 o 2 The dosage is 0.4%, H 2 o 2 :Fe 2+ =2:1, the Venturi dosing position is located at 2 / 3 of the reactor elevation; use NaOH solution to adjust the pH to about 8, and enter the vertical flow sedimentation tank 06 for precipitation and separation. The effluent water quality of each process is shown in Table 1. The distillation conc...
Embodiment 2
[0053] The same procedure was carried out as described in Example 1. Wastewater COD is 30000mg / L, pH is 7, TOC is 5000mg / L, hardness is 300mg / L (as CaCO 3 count). Use NaOH solution to adjust the pH to 6, and the waste water begins to evaporate at a negative pressure (40kPa) and a temperature of 90°C; the ozone catalyst MnO in the reactor 2 The dosage is 400mg / L, the dosage of ozone is 5mg / L, the concentration of ozone introduced is 120mg / L, and the hydraulic retention time is 90min; H 2 o 2 The dosage is 0.6%, H 2 o 2 :Fe 2+ = 4:1, Venturi injection position is located at 1 / 3 from the bottom of the reactor. The distillation concentration rate of the final emulsified waste liquid is 19, and the recovery rate of clear water reaches 95%. The effluent after precipitation has low salt, low concentration, and low hardness, which meets the requirements of self-reuse. The effluent from the vertical flow sedimentation tank 06 enters the clear water tank. The effluent water qual...
Embodiment 3
[0057] The same operation was carried out as described in Example 1, but the treated water was different, and the control conditions and parameters were different. Use NaOH solution to adjust the pH to 5.5, and the wastewater starts to evaporate into water vapor at 60kPa and 80°C; the ozone catalyst MnO 2 The dosage is 250mg / L, the dosage of ozone is 3mg / L, the concentration of ozone introduced is 90mg / L, and the hydraulic retention time is 60min; H 2 o 2 The dosage is 0.5%, H 2 o 2 :Fe 2+ =3:1, the dosing position is located 1 / 2 away from the bottom of multi-stage combined advanced oxidation reactor 03. See Table 3 for the effluent quality of each stage of the process. The recovery rate of distilled water from the final emulsified waste liquid reaches 92%, and the effluent after precipitation meets the requirements of self-reuse.
[0058] Table 3 Water quality analysis table of each process effluent
[0059]
PUM
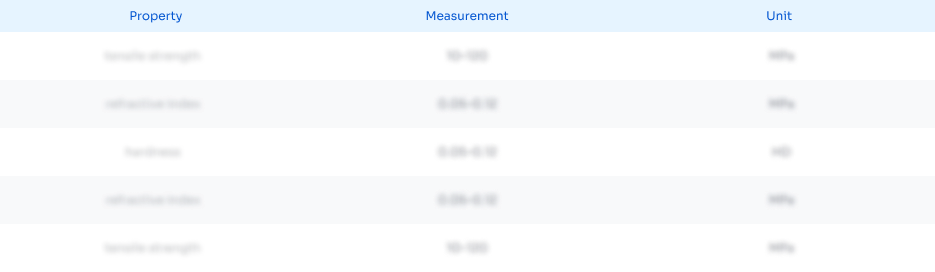
Abstract
Description
Claims
Application Information

- R&D Engineer
- R&D Manager
- IP Professional
- Industry Leading Data Capabilities
- Powerful AI technology
- Patent DNA Extraction
Browse by: Latest US Patents, China's latest patents, Technical Efficacy Thesaurus, Application Domain, Technology Topic, Popular Technical Reports.
© 2024 PatSnap. All rights reserved.Legal|Privacy policy|Modern Slavery Act Transparency Statement|Sitemap|About US| Contact US: help@patsnap.com