Scanning/molding method for improving additive manufacturing/molding quality of metal part
A molding method and additive manufacturing technology, applied in the field of scanning molding, can solve the problems of low molding efficiency, uneven powder laying, affecting the quality of powder laying, etc., so as to improve the density, reduce thermal stress, and reduce the probability of warping defects. Effect
- Summary
- Abstract
- Description
- Claims
- Application Information
AI Technical Summary
Problems solved by technology
Method used
Image
Examples
Embodiment
[0033] Such as figure 1 As shown, after the laser beam is focused by the metal additive manufacturing equipment, a processing point with concentrated energy (focused laser spot 1) will be obtained, and the metal powder will be melted through the processing point. However, there is a heat-affected zone at the processing point, which makes the forming melt channel wider than the processing point. The size of the forming melt channel 2 is a relatively important parameter, and the scanning parameters should be adjusted according to the size in the scanning forming.
[0034] Especially when scanning the contours of supports and parts, processing compensation is required, and the compensation value is usually set to half the size of the forming melt channel 2.
[0035] Such as figure 2 and image 3 As shown, if the laser spot compensation is not set during processing, when scanning the edge of the contour, the scanning track 5 at the center of the laser spot coincides with the t...
PUM
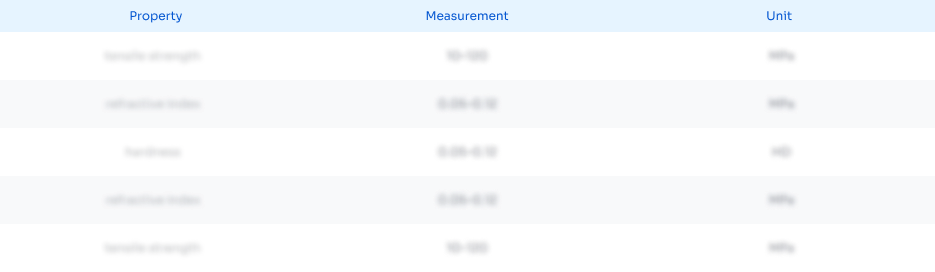
Abstract
Description
Claims
Application Information

- R&D
- Intellectual Property
- Life Sciences
- Materials
- Tech Scout
- Unparalleled Data Quality
- Higher Quality Content
- 60% Fewer Hallucinations
Browse by: Latest US Patents, China's latest patents, Technical Efficacy Thesaurus, Application Domain, Technology Topic, Popular Technical Reports.
© 2025 PatSnap. All rights reserved.Legal|Privacy policy|Modern Slavery Act Transparency Statement|Sitemap|About US| Contact US: help@patsnap.com