Aircraft hanging-type fluxgate magnetic gradient tensor instrument correction method
A correction method and fluxgate technology, applied in the direction of instruments, measuring devices, measuring electrical variables, etc., can solve problems such as inability to guarantee correctness, difficulty in finding areas with uniform magnetic fields, submerging target magnetic detection signals, etc.
- Summary
- Abstract
- Description
- Claims
- Application Information
AI Technical Summary
Problems solved by technology
Method used
Image
Examples
Embodiment Construction
[0065] The present invention will be further described in detail below in conjunction with the accompanying drawings and embodiments.
[0066] The present invention utilizes the characteristic that the gradient tensor of the earth's magnetic field in the high altitude is approximately zero to perform correction, and then calculates the high-altitude correction according to the fact that the invariant of the tensor meter rotation in the non-zero area of the ground magnetic gradient can indicate the inconsistency of the scale factors of each gradient component Finally, the scale factor of each gradient component that has not been determined finally achieves the purpose of calibrating the fluxgate tensor.
[0067] Based on the single fluxgate error model, the present invention derives the error model of the fluxgate tensor, and then utilizes the characteristic that the gradient tensor of the earth's magnetic field in the high altitude is approximately zero, and the invariant for...
PUM
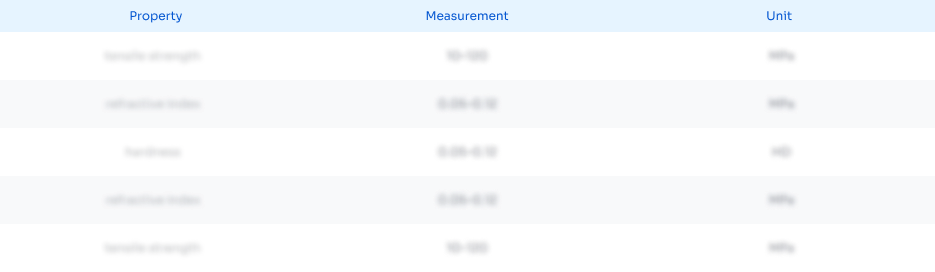
Abstract
Description
Claims
Application Information

- R&D
- Intellectual Property
- Life Sciences
- Materials
- Tech Scout
- Unparalleled Data Quality
- Higher Quality Content
- 60% Fewer Hallucinations
Browse by: Latest US Patents, China's latest patents, Technical Efficacy Thesaurus, Application Domain, Technology Topic, Popular Technical Reports.
© 2025 PatSnap. All rights reserved.Legal|Privacy policy|Modern Slavery Act Transparency Statement|Sitemap|About US| Contact US: help@patsnap.com