Manufacturing method of anti-microbial satin fabric
A satin fabric and velvet technology, applied in the field of textile fabrics, can solve the problem of neglecting the antibacterial of the fabric, and achieve the effects of excellent moisture absorption and perspiration, good air permeability and increased drape.
- Summary
- Abstract
- Description
- Claims
- Application Information
AI Technical Summary
Problems solved by technology
Method used
Examples
Embodiment 1
[0030] A preparation method for antibacterial satin fabric, comprising the following steps:
[0031] A. Weaving: use superfine polyester fiber and modified cattail fiber as raw materials, and use water jet loom to make gray cloth;
[0032] B, sizing and oiling: the gray cloth prepared in step A is subjected to sizing and oiling;
[0033] C. Desizing and refining: use a low bath ratio high pressure jet overflow machine for desizing and refining treatment, the process prescription and conditions are as follows: desizing bath PH value 8, refining agent: 3g / L, NaOH: 1.5g / L, liquor ratio : 1:12, temperature: 78°C, time: 38min;
[0034] D. Alkali weight reduction: After the desizing and refining is completed, then carry out alkali weight reduction treatment. The treatment conditions are 35% NaOH 120g / L, temperature: 105°C, time: 8min;
[0035] E. Post-setting drying: first soak in 3% sodium dodecylsulfonate solution for 8 minutes, then perform 100°C water padding, and then dry and...
Embodiment 2
[0048] A preparation method for antibacterial satin fabric, comprising the following steps:
[0049] A. Weaving: use superfine polyester fiber and modified cattail fiber as raw materials, and use water jet loom to make gray cloth;
[0050] B, sizing and oiling: the gray cloth prepared in step A is subjected to sizing and oiling;
[0051] C. Desizing and refining: use a low bath ratio high-pressure jet overflow machine for desizing and refining treatment. The process prescription and conditions are as follows: desizing bath PH value 7.5-8.5, refining agent: 2g / L, NaOH: 1g / L, bath Ratio: 1:15, temperature: 80°C, time: 35min;
[0052] D. Alkali weight reduction: After desizing and refining, carry out alkali weight reduction treatment. The treatment conditions are 35% NaOH 140g / L, temperature: 110°C, time: 10min;
[0053]E. Post-setting drying: first soak in 5% sodium dodecylsulfonate solution for 10 minutes, then perform 100°C water padding, and then dry and shape at 190°C;
...
Embodiment 3
[0066] A preparation method for antibacterial satin fabric, comprising the following steps:
[0067] A. Weaving: use superfine polyester fiber and modified cattail fiber as raw materials, and use water jet loom to make gray cloth;
[0068] B, sizing and oiling: the gray cloth prepared in step A is subjected to sizing and oiling;
[0069] C. Desizing and refining: use a low bath ratio high-pressure jet overflow machine for desizing and refining treatment. The process prescription and conditions are as follows: desizing bath PH value 7.5-8.5, refining agent: 2g / L, NaOH: 2g / L, bath Ratio: 1:10, temperature: 75-80°C, time: 35-40min;
[0070] D. Alkali reduction: After desizing and refining, carry out alkali reduction treatment. The treatment conditions are 35% NaOH 100g / L, temperature: 100°C, time: 5min;
[0071] E. Post-setting drying: first soak in 5% sodium dodecylsulfonate solution for 5 minutes, then perform padding in 100°C water, and then dry and shape at 190°C;
[0072]...
PUM
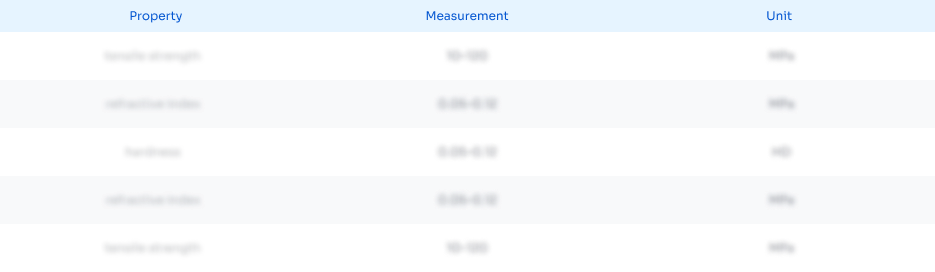
Abstract
Description
Claims
Application Information

- Generate Ideas
- Intellectual Property
- Life Sciences
- Materials
- Tech Scout
- Unparalleled Data Quality
- Higher Quality Content
- 60% Fewer Hallucinations
Browse by: Latest US Patents, China's latest patents, Technical Efficacy Thesaurus, Application Domain, Technology Topic, Popular Technical Reports.
© 2025 PatSnap. All rights reserved.Legal|Privacy policy|Modern Slavery Act Transparency Statement|Sitemap|About US| Contact US: help@patsnap.com