Method for preparing diatomite hollow fiber ceramic membrane
A diatomite and ceramic membrane technology, applied in chemical instruments and methods, membrane technology, semi-permeable membrane separation, etc., can solve the problems of high raw material cost and high sintering temperature, and achieve scientific and reasonable methods, strong applicability, and good effects. Effect
- Summary
- Abstract
- Description
- Claims
- Application Information
AI Technical Summary
Problems solved by technology
Method used
Image
Examples
Embodiment 1
[0026] Add 5g of polymer polyethersulfone (PES), 7.5g of porogen polyethylene glycol (PEG1000) into 65g of organic solvent N,N-dimethylacetamide (DMAc), and heat in a water bath at 75°C , mechanically stirred for 6 h to fully dissolve the polymer.
[0027] Add 30.5g of diatomaceous earth and 28g of alumina to the polymer solution as inorganic particles and 4g of low-temperature sintering aid V required for sintering 2 o 5 , continue to heat in a constant temperature water bath and mechanically stir for 24 h to obtain a casting solution.
[0028] Put the prepared casting liquid into the slurry tank of the spinning machine, vacuumize at 60° C. for 4 hours to remove residual air bubbles, and let it stand for 20 hours for defoaming. Install the prepared hollow fiber liner in the spinning head, adjust the extrusion rate of the casting solution to 2mL / min, the extrusion rate of the liner to 2cm / min, adjust the air distance to 2cm, and set the temperature of the coagulation bath to...
Embodiment 2
[0032] Add 22.5g of polymer polysulfone (PS) and 7.5g of porogen polyethylene glycol (PEG400) into 67.5g of organic solvent N-methylpyrrolidone (NMP), heat in a water bath at 70°C, and stir mechanically 4 h to fully dissolve the polymer.
[0033] Add 24.3g of diatomaceous earth and 20.7g of alumina as inorganic particles and 7.5g of low-temperature sintering aid AlF required for sintering into the polymer solution 3 , continue to heat in a constant temperature water bath and mechanically stir for 20 h to obtain a casting solution.
[0034] Put the prepared casting solution into the slurry tank of the spinning machine, vacuumize at 65° C. for 5 hours to remove residual air bubbles, and let it stand for 20 hours for defoaming. Install the prepared hollow fiber liner in the spinning head, adjust the extrusion rate of the casting solution to 2mL / min, the extrusion rate of the liner to 2cm / min, adjust the air distance to 2cm, and set the temperature of the coagulation bath to 20 °C...
Embodiment 3
[0038] Mix 15g of polymer: polyvinylidene fluoride (PVDF), 7.5g porogen K 30 , was added to 65g of organic solvent N-methylpyrrolidone (NMP), heated in a water bath at 65°C, and mechanically stirred for 5 hours to fully dissolve the polymer.
[0039] Add 30.5g of diatomite and 28g of alumina to the polymer solution as inorganic particles and 4g of low-temperature sintering aid CaCO required for sintering 3 , continue to heat in a constant temperature water bath and mechanically stir for more than 22 h to obtain a casting solution.
[0040] Put the prepared casting solution into the slurry tank of the spinning machine, vacuumize at 60° C. for 4 hours to remove residual bubbles, and let it stand for 20 hours for defoaming. Install the prepared hollow fiber liner in the spinning head, adjust the extrusion rate of the casting solution to 2mL / min, the extrusion rate of the liner to 2cm / min, adjust the air distance to 2cm, and set the temperature of the coagulation bath to 20 °C f...
PUM
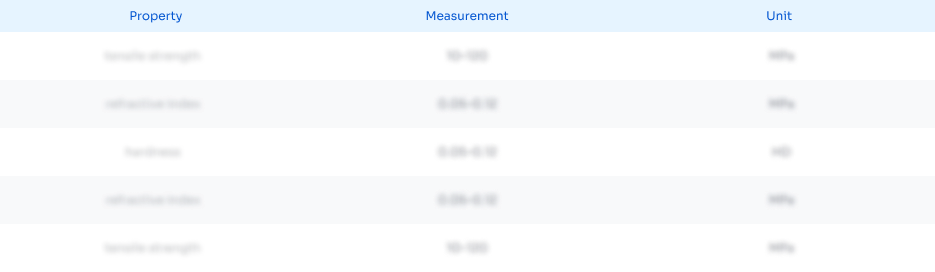
Abstract
Description
Claims
Application Information

- R&D
- Intellectual Property
- Life Sciences
- Materials
- Tech Scout
- Unparalleled Data Quality
- Higher Quality Content
- 60% Fewer Hallucinations
Browse by: Latest US Patents, China's latest patents, Technical Efficacy Thesaurus, Application Domain, Technology Topic, Popular Technical Reports.
© 2025 PatSnap. All rights reserved.Legal|Privacy policy|Modern Slavery Act Transparency Statement|Sitemap|About US| Contact US: help@patsnap.com