A kind of manufacturing method of multifunctional flame-retardant polyester fabric
A flame-retardant polyester and manufacturing method technology, applied in the field of functional textile materials, can solve the problems of single function, easy perforation and droplet
- Summary
- Abstract
- Description
- Claims
- Application Information
AI Technical Summary
Problems solved by technology
Method used
Image
Examples
Embodiment 1
[0022] Pad the polyester fabric dyed with warning fluorescent high temperature at 100-130°C in the first step of padding liquid, then pre-bake the polyester fabric at 110°C-130°C for 3 minutes, and then bake it at 160°C-180°C for 3 minutes , After the fabric is shaped and cooled, the reverse side of the fabric is subjected to high temperature oil surface calendering at 140°C-160°C for 3 times, and the weight of the polyester fabric increases by 0.8% after the treatment is completed.
[0023] Wherein said first step padding solution is calculated and composed as follows in parts by mass:
[0024]
[0025] Then, on the calendered side of the polyester fabric, apply the second-step primer liquid, and after forming a uniform adhesive film on the surface of the polyester fabric, place the polyester fabric at 140-160°C for baking for 5 minutes , After the treatment is completed, the polyester fabric weight increases by 6%.
[0026] Wherein said second step primer slurry is count...
Embodiment 2
[0036] Pad the polyester fabric dyed with warning fluorescent high temperature at 100-130°C in the first padding liquid, then pre-dry the polyester fabric at 110°C-120°C for 1.5 minutes, and then bake it at 160°C-180°C for 1.5 minutes , After the fabric is shaped and cooled, then the reverse side of the fabric is subjected to high temperature oil surface calendering at 100°C-160°C for 2 times; after the treatment is completed, the weight of the polyester fabric increases by 0.5%.
[0037] Wherein said first step padding solution is calculated and composed as follows in parts by mass:
[0038]
[0039] Then, on the calendered side of the polyester fabric, apply the second-step primer liquid, and after forming a uniform adhesive film on the surface of the polyester fabric, place the polyester fabric at 140-150°C for baking, and the baking time needs 3 Minutes; 4% increase in weight of polyester fabric after gluing.
[0040] Wherein said second step primer slurry is counted a...
Embodiment 3
[0050] Pad the polyester fabric dyed with warning fluorescent high temperature at 120-130°C in the first step of padding liquid, then pre-dry the polyester fabric at 110°C-120°C for 2 minutes, and then bake it at 160°C-180°C for 2 minutes , After the fabric is shaped and cooled, the reverse side of the fabric is subjected to high temperature oil surface calendering at 140°C-150°C for 3 times; after the treatment is completed, the weight of the polyester fabric increases by 1%.
[0051] Wherein said first step padding solution is calculated and composed as follows in parts by mass:
[0052]
[0053] Then, on the calendered side of the polyester fabric, apply the second-step primer liquid, and after forming a uniform adhesive film on the surface of the polyester fabric, place the polyester fabric at 130-140°C for baking, and the baking time needs 3 Minutes; 5% increase in weight of polyester fabric after gluing.
[0054]Wherein said second step primer slurry is counted and c...
PUM
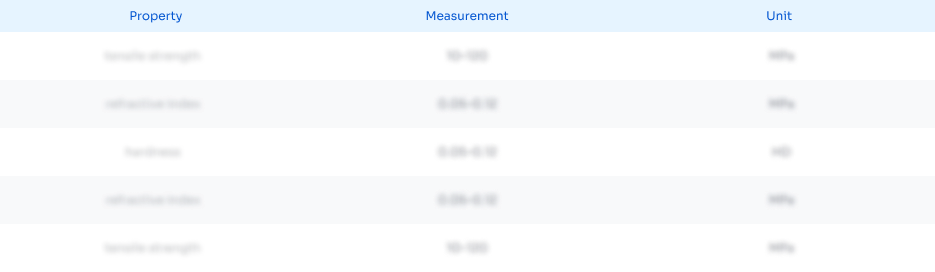
Abstract
Description
Claims
Application Information

- Generate Ideas
- Intellectual Property
- Life Sciences
- Materials
- Tech Scout
- Unparalleled Data Quality
- Higher Quality Content
- 60% Fewer Hallucinations
Browse by: Latest US Patents, China's latest patents, Technical Efficacy Thesaurus, Application Domain, Technology Topic, Popular Technical Reports.
© 2025 PatSnap. All rights reserved.Legal|Privacy policy|Modern Slavery Act Transparency Statement|Sitemap|About US| Contact US: help@patsnap.com