Method for preparing self-heating material for central heating unit
A central heating and self-heating technology, applied in the direction of heat exchange materials, chemical instruments and methods, etc., can solve the problems of short service life, inability to apply central heating units, and slow heat release, so as to prolong the service life and facilitate separate storage , the effect of resistance reduction
- Summary
- Abstract
- Description
- Claims
- Application Information
AI Technical Summary
Problems solved by technology
Method used
Examples
Embodiment 1
[0022] 1) Add polyacrylamide and distilled water into the container at a mass ratio of 8:92, heat to 94°C, stir until completely dissolved, cool to gel, and obtain product A;
[0023] 2) Mix product A, potassium chloride, sodium dodecylbenzenesulfonate and iron powder according to the mass ratio of 10:6:5:80 and then granulate to obtain gel particles, which are called product B; and,
[0024] Product A, zinc powder, potassium chloride and sodium dodecylbenzenesulfonate are mixed according to a mass ratio of 10:80:6:6 and then granulated to obtain gel particles, which are called product C;
[0025] 3) When using, mix product B and product C according to the mass ratio of 1:1 to obtain self-heating materials for central heating units.
Embodiment 2
[0027] 1) Add sodium alginate and distilled water into the container according to the mass ratio of 3:97, heat to 80°C, stir until completely dissolved, cool to gel, and obtain product A;
[0028] 2) Mix product A, potassium sulfate, sodium lauryl sulfate and iron powder according to the mass ratio of 5:1:10:93 and then granulate to obtain gel particles, which are called product B; and,
[0029] Product A, magnesium powder, potassium sulfate and sodium lauryl sulfate are mixed according to a mass ratio of 15:65:10:1 and then granulated to obtain gel particles, which are called product C;
[0030] 3) When using, mix product B and product C according to the mass ratio of 15:85 to obtain self-heating materials for central heating units.
Embodiment 3
[0032] 1) Add gelatin and distilled water into the container according to the mass ratio of 15:60, heat to 98°C, stir until completely dissolved, cool to gel, and obtain product A;
[0033] 2) Mix product A, sodium sulfate, sorbitan fatty acid ester-20 and iron powder according to the mass ratio of 15:10:1:65 and then granulate to obtain gel particles, which are called product B; and,
[0034] Product A, lead powder, sodium sulfate and sorbitan fatty acid ester-20 are mixed according to a mass ratio of 5:93:1:10 and then granulated to obtain gel particles, which are called product C;
[0035] 3) When using, mix product B and product C according to the mass ratio of 85:15 to obtain self-heating materials for central heating units.
PUM
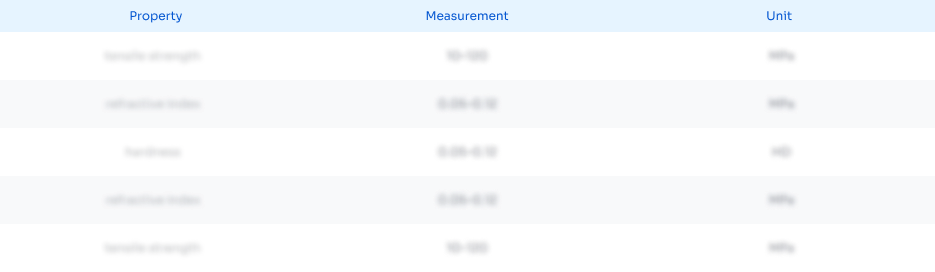
Abstract
Description
Claims
Application Information

- Generate Ideas
- Intellectual Property
- Life Sciences
- Materials
- Tech Scout
- Unparalleled Data Quality
- Higher Quality Content
- 60% Fewer Hallucinations
Browse by: Latest US Patents, China's latest patents, Technical Efficacy Thesaurus, Application Domain, Technology Topic, Popular Technical Reports.
© 2025 PatSnap. All rights reserved.Legal|Privacy policy|Modern Slavery Act Transparency Statement|Sitemap|About US| Contact US: help@patsnap.com