Thermal deformation-discordant single-rotor double-thrust bearing axial force testing method
A test method and technology of axial force, applied in the direction of force/torque/power measuring instrument, measuring device, instrument, etc., can solve the research report on single-rotor double thrust bearing test technology that has not been seen, and the two thrust bearings cannot be synchronized Test and other issues, to achieve accurate and reliable test results, easy test results
- Summary
- Abstract
- Description
- Claims
- Application Information
AI Technical Summary
Problems solved by technology
Method used
Image
Examples
Embodiment 1
[0060] This embodiment provides a method for testing the axial force of a single-rotor double-thrust bearing with uncoordinated thermal deformation. Single-rotor double-thrust bearing secondary measurement engine modification and assembly process of electric measurement technology.
[0061] The analysis method of temperature deformation incompatibility quantity based on the two-test method is established.
[0062] A data analysis method for the total axial force of double thrust bearings was established.
[0063]According to the test results, the assembly process of double thrust bearing bearing axial force is established.
[0064] Technical problem to be solved:
[0065] Single-rotor double-thrust bearing secondary measurement engine modification and assembly process;
[0066] Analytical method of deformation incongruity caused by temperature;
[0067] Data analysis method of total axial force of double thrust bearing;
[0068] According to the test results, an assembly ...
PUM
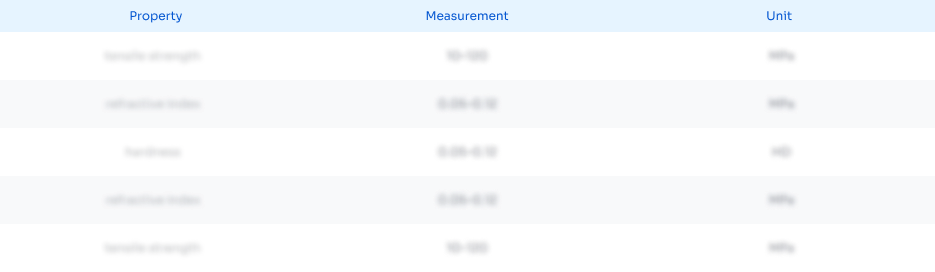
Abstract
Description
Claims
Application Information

- R&D Engineer
- R&D Manager
- IP Professional
- Industry Leading Data Capabilities
- Powerful AI technology
- Patent DNA Extraction
Browse by: Latest US Patents, China's latest patents, Technical Efficacy Thesaurus, Application Domain, Technology Topic, Popular Technical Reports.
© 2024 PatSnap. All rights reserved.Legal|Privacy policy|Modern Slavery Act Transparency Statement|Sitemap|About US| Contact US: help@patsnap.com