An eddy current displacement sensor and its implementation method
A technology of displacement sensor and realization method, which is applied to instruments, electrical devices, electromagnetic means, etc., can solve the problems of small variation range of output signal of inductance probe, low anti-interference, complex system, etc., to improve frequency response performance, The effect of reducing the sampling rate and high precision
- Summary
- Abstract
- Description
- Claims
- Application Information
AI Technical Summary
Problems solved by technology
Method used
Image
Examples
Embodiment Construction
[0031] In order to make the object, technical solution and advantages of the present invention clearer, the present invention will be further described in detail below in conjunction with the embodiments and accompanying drawings.
[0032] like figure 1 As shown, the structure of the large-range, high-precision and high-dynamic-response eddy-current displacement sensor includes: AC resonant booster bridge, amplitude stabilization circuit, amplitude compensation and addition circuit, quadrature sampling trigger signal generation circuit and high-speed sampling processor; described
[0033] The AC resonant step-up bridge is made up of a resonator, a resistor R2 connected in parallel with the resonator, and a capacitor C1 and a resistor R1 connected in series with the resonator; the resonator is made up of an inductance probe Lx and two series capacitors C2 and C3;
[0034] The amplitude stabilization circuit is composed of a variable gain amplifier 4, a synchronous detection ci...
PUM
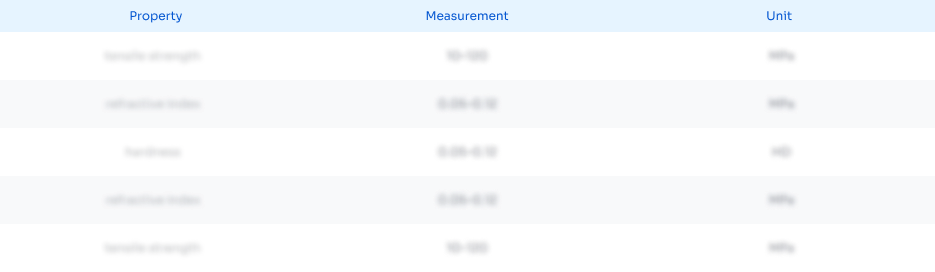
Abstract
Description
Claims
Application Information

- Generate Ideas
- Intellectual Property
- Life Sciences
- Materials
- Tech Scout
- Unparalleled Data Quality
- Higher Quality Content
- 60% Fewer Hallucinations
Browse by: Latest US Patents, China's latest patents, Technical Efficacy Thesaurus, Application Domain, Technology Topic, Popular Technical Reports.
© 2025 PatSnap. All rights reserved.Legal|Privacy policy|Modern Slavery Act Transparency Statement|Sitemap|About US| Contact US: help@patsnap.com