A method for producing fine ceramic products using waste ceramics as the main material
A technology of fine ceramics and waste ceramics, applied in the field of ceramics manufacturing, can solve problems such as cracking, and achieve the effect of high degree of porcelainization, full utilization of resources, and high degree of delicacy
- Summary
- Abstract
- Description
- Claims
- Application Information
AI Technical Summary
Problems solved by technology
Method used
Image
Examples
Embodiment 1
[0012] (1) Put the waste ceramics into the ball mill, and based on the weight of the waste ceramics, add 2% of zinc oxide, 2% of titanium dioxide, 0.3% of absolute ethanol and 2.0% of oleic acid and ball mill for 15 hours until the median diameter of the mixed powder is 10-18um;
[0013] (2) After the mixed powder is sieved, add paraffin wax with 8% weight of waste ceramics to make blocks;
[0014] (3) Heat and melt the block, send it to the die-casting machine and inject it into the metal mold under 0.5MPa pressure;
[0015] (4) Degrease and biscuit at 800°C after demoulding;
[0016] (5) The biscuit-fired green body is put into the kiln according to the traditional color glaze decoration process and fired at 1250°C to obtain the finished product.
Embodiment 2
[0018] (1) Put the waste ceramics into the ball mill, and based on the weight of the waste ceramics, add 2% zinc oxide, 4% titanium dioxide, 1.0% absolute ethanol and 1.0% oleic acid and ball mill for 15 hours until the median diameter of the mixed powder is 10-18um;
[0019] (2) After the mixed powder is sieved, add paraffin wax with 10% weight of waste ceramics to make blocks;
[0020] (3) Heat and melt the block, send it to the die-casting machine and inject it into the metal mold under 0.5MPa pressure;
[0021] (4) Degrease and biscuit at 900°C after demoulding;
[0022] (5) The biscuit-fired green body is traditionally glazed with green glaze and high-temperature kiln glaze, and the firing temperature is 1300°C to obtain the finished product.
Embodiment 3
[0024] (1) Put the waste ceramics into the ball mill, based on the weight of the waste ceramics, add 5% zinc oxide, 2% titanium dioxide, 1.0% absolute ethanol and 1.0% oleic acid and ball mill for 15 hours until the median diameter of the mixed powder is 10-18um;
[0025] (2) After the mixed powder is sieved, add paraffin wax with 10% weight of waste ceramics to make blocks;
[0026] (3) Heat and melt the block, send it to the die-casting machine and inject it into a metal mold under a pressure of 0.5MPa, and the injection temperature is 80°C;
[0027] (4) Degrease and biscuit at 900°C after demoulding;
[0028] (5) Glaze the bisque-fired body to obtain an over-glaze painted porcelain body, and put it into a kiln for firing at 1300°C to obtain a finished product.
PUM
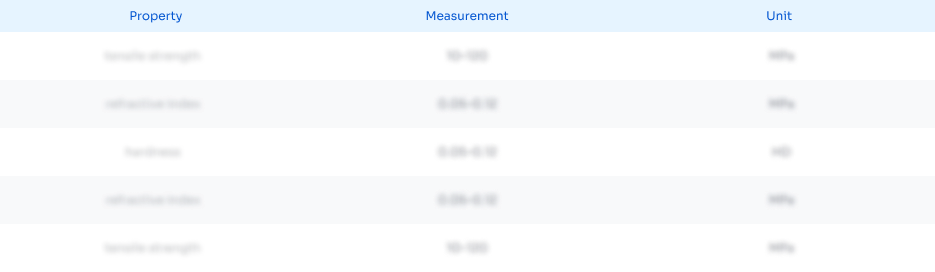
Abstract
Description
Claims
Application Information

- R&D
- Intellectual Property
- Life Sciences
- Materials
- Tech Scout
- Unparalleled Data Quality
- Higher Quality Content
- 60% Fewer Hallucinations
Browse by: Latest US Patents, China's latest patents, Technical Efficacy Thesaurus, Application Domain, Technology Topic, Popular Technical Reports.
© 2025 PatSnap. All rights reserved.Legal|Privacy policy|Modern Slavery Act Transparency Statement|Sitemap|About US| Contact US: help@patsnap.com