An air compressor split type three-stage oil-gas separation device
A separation device and split-type technology, which is applied in the direction of combined devices, separation methods, and dispersed particle separation, can solve the problems of low oil-gas separation efficiency, difficulty in manufacturing cyclone separation cylinders and filter element separation cylinders, and impossibility of using filter element separation cylinders. Cyclone method and other problems, to achieve the effect of improving filtration accuracy and operation stability, fine oil-gas separation effect, and outstanding oil-gas separation performance
- Summary
- Abstract
- Description
- Claims
- Application Information
AI Technical Summary
Problems solved by technology
Method used
Image
Examples
Embodiment
[0038] Combine figure 2 As shown, an air compressor split three-stage oil and gas separation device of this embodiment includes a first oil and gas barrel 1 and a second oil and gas barrel 2 separately arranged, a gas outlet of the first oil and gas barrel 1 and a second oil and gas barrel 2 The gas inlets are connected by the oil and gas pipeline 3. The first oil and gas barrel 1 is used for primary oil and gas separation, and its main function is to store oil, and the second oil and gas barrel 2 is used for secondary and tertiary oil and gas separation, and its main function is fine It separates oil and gas and can also be used as a buffer gas tank. In this embodiment, the oil and gas separation device is cleverly designed into two parts, the first oil and gas barrel 1 and the second oil and gas barrel 2, which are separately arranged. The volume of the first oil and gas barrel 1 and the second oil and gas barrel 2 is lighter, easier to manufacture, and more layout. Flexible...
PUM
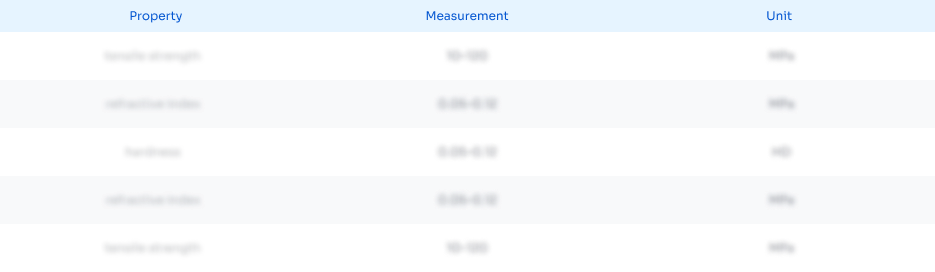
Abstract
Description
Claims
Application Information

- Generate Ideas
- Intellectual Property
- Life Sciences
- Materials
- Tech Scout
- Unparalleled Data Quality
- Higher Quality Content
- 60% Fewer Hallucinations
Browse by: Latest US Patents, China's latest patents, Technical Efficacy Thesaurus, Application Domain, Technology Topic, Popular Technical Reports.
© 2025 PatSnap. All rights reserved.Legal|Privacy policy|Modern Slavery Act Transparency Statement|Sitemap|About US| Contact US: help@patsnap.com