Dedusting device for cement plants
A dust removal device and a technology for a cement plant, applied in the field of cement manufacturing, can solve the problems of not being able to exhaust and dredging pipes by themselves, endangering the health of workers on the post, and aggravating pipe blockages, etc.
- Summary
- Abstract
- Description
- Claims
- Application Information
AI Technical Summary
Problems solved by technology
Method used
Image
Examples
Embodiment Construction
[0028] see figure 1 , is a preferred embodiment of a dust removal device used in a cement plant, including a first air inlet hopper 1, a second air inlet hopper 2, an air extraction pipe 3, an exhaust pipe 4, and an air supply pipe 5 for providing dust removal Power primary vacuum pump 6, secondary vacuum pump 7, first filter 8 and second filter 9 for filtering cement ash. Preferably, the casings of the primary and secondary vacuum pumps 7 are manufactured in one piece, with a high degree of integration, smaller space occupation, and convenient installation and transportation. Further preferably, the casings of the primary and secondary vacuum pumps 7 are respectively provided with cooling air ducts 10, one end of the cooling air ducts 10 communicates with the pump cavity of the corresponding vacuum pump, and the other end is connected to the air filter 11, and the cooling air The pipe 10 is provided with a cooling air one-way valve, so that the cooling air enters the pump ch...
PUM
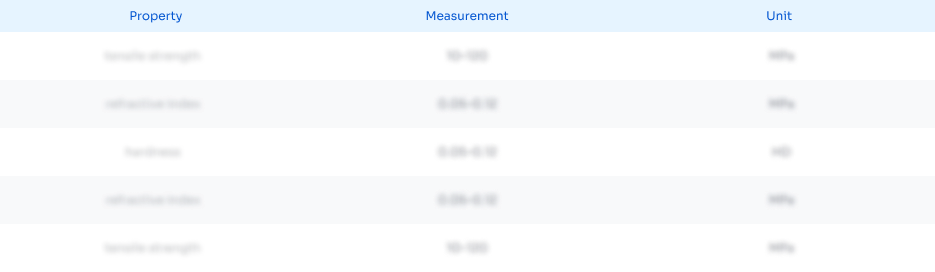
Abstract
Description
Claims
Application Information

- Generate Ideas
- Intellectual Property
- Life Sciences
- Materials
- Tech Scout
- Unparalleled Data Quality
- Higher Quality Content
- 60% Fewer Hallucinations
Browse by: Latest US Patents, China's latest patents, Technical Efficacy Thesaurus, Application Domain, Technology Topic, Popular Technical Reports.
© 2025 PatSnap. All rights reserved.Legal|Privacy policy|Modern Slavery Act Transparency Statement|Sitemap|About US| Contact US: help@patsnap.com