A Multilayer Electrode Displacement Sensor
A displacement sensor, multi-layer electrode technology, applied in the field of sensors, can solve the problems of flexible FPC deformation, terminal alignment difficulties, etc., to save costs, avoid alignment difficulties, and improve compactness.
- Summary
- Abstract
- Description
- Claims
- Application Information
AI Technical Summary
Problems solved by technology
Method used
Image
Examples
specific Embodiment approach 1
[0038] Such as Figure 1a and Figure 1b The capacitive grid angular displacement sensor 100 shown includes an emitter electrode substrate 110 , a coupling electrode substrate 120 , a wiring board 130 and a detection circuit 140 . The emitter electrode substrate 110 is a glass substrate, and the grid-shaped emitter electrode group 111 and the receiver electrode 113 are prepared on the same surface of the emitter electrode substrate 110, and each emitter electrode of the grid-like emitter electrode group 111 has an emitter electrode lead-out terminal , the outgoing terminals of each transmitting electrode form the transmitting electrode outgoing terminal group 112, and the receiving electrode 113 has a receiving electrode outgoing terminal 114; the coupling electrode substrate 120 is also a glass substrate, and the grid-shaped coupling electrode group 121 is prepared on the coupling electrode substrate 120, the coupling electrode group 121 transmits the electrical signal on the...
specific Embodiment approach 2
[0042] Such as Figure 2a and Figure 2b The capacitive grid angular displacement sensor 200 shown includes an emitter electrode substrate 210 , a coupling electrode substrate 220 , a wiring board 230 and a detection circuit 240 . The emitter electrode substrate 210 is a glass substrate, and the grid-shaped emitter electrode group 211 and the receiver electrode 213 are prepared on the same surface of the emitter electrode substrate 210, and each emitter electrode of the grid-like emitter electrode group 211 has an emitter electrode lead-out terminal position respectively. , the outgoing terminals of each transmitting electrode form the transmitting electrode outgoing terminal group 212, and the receiving electrode 213 has a receiving electrode outgoing terminal 214; the coupling electrode substrate 220 is also a glass substrate, and the gear-shaped coupling electrode 221 is prepared on the coupling electrode substrate 220 On, the coupling electrode 221 transmits the electrica...
specific Embodiment approach 3
[0046] Such as Figure 3a and Figure 3b The capacitive grid angular displacement sensor 300 shown includes an emitter electrode substrate 310 , a coupling electrode substrate 320 , a wiring board 330 and a detection circuit 340 . The emitter electrode substrate 310 is a ceramic material substrate, and the grid-shaped emitter electrode group 311 and the receiver electrode 313 are prepared on the same surface of the emitter electrode substrate 310, and each emitter electrode of the grid-like emitter electrode group 311 has an emitter electrode lead-out terminal position respectively. , the outgoing terminals of each transmitting electrode form the transmitting electrode outgoing terminal group 312, and the receiving electrode 313 has a receiving electrode outgoing terminal 314; the coupling electrode substrate 320 is also a ceramic material substrate, and the grid-shaped coupling electrode group 321 is prepared on the coupling electrode substrate 320, the coupling electrode gr...
PUM
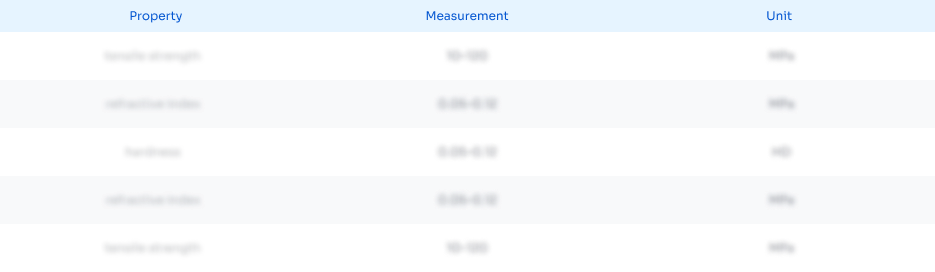
Abstract
Description
Claims
Application Information

- R&D Engineer
- R&D Manager
- IP Professional
- Industry Leading Data Capabilities
- Powerful AI technology
- Patent DNA Extraction
Browse by: Latest US Patents, China's latest patents, Technical Efficacy Thesaurus, Application Domain, Technology Topic, Popular Technical Reports.
© 2024 PatSnap. All rights reserved.Legal|Privacy policy|Modern Slavery Act Transparency Statement|Sitemap|About US| Contact US: help@patsnap.com