A gapless force transmission coupling device that can generate shear deformation in a supergravity field
A technology of shear deformation and supergravity field, applied in the direction of couplings, slip couplings, mechanical equipment, etc., can solve the problems of inability to produce flexible shear deformation, force transmission distortion, difference, etc., to ensure no distortion Passing, the effect that is conducive to normal work
- Summary
- Abstract
- Description
- Claims
- Application Information
AI Technical Summary
Problems solved by technology
Method used
Image
Examples
Embodiment 1
[0026] Such as figure 1 As shown, the gapless force transmission coupling device includes three rubber layers 2 and two steel plates 4, the balls 3 in each rubber layer 2 are evenly distributed in four layers in the direction perpendicular to the force transmission direction, and other structures are the same as those mentioned above. The related structure is the same.
Embodiment 2
[0028] Such as figure 2 As shown, the non-gap force transmission coupling device includes two rubber layers 2 and a steel plate 4, and other structures are the same as those in Embodiment 1.
Embodiment 3
[0030] Such as image 3 As shown, the gapless force transmission coupling device includes four rubber layers 2 and three steel plates 4 in total, and other structures are the same as those in Embodiment 1.
[0031] The quantity of the rubber layer 2 and the steel plate 4 is determined according to the distance between the piston rod of the hydraulic cylinder and the vibration table, the thickness of the rubber layer 2 and the thickness of the steel plate 4 .
[0032] combine Figure 1-Figure 4 , the working principle of the gapless force transmission coupling device that can produce shear deformation in the supergravity field of the present invention is as follows:
[0033] 1. Axial gapless force transmission:
[0034] Such as figure 1 As shown, the axial transmission path of the thrust output by the piston rod of the hydraulic cylinder is: the first connecting flange 1, the first row of balls 3, the first steel plate 4, the second row of balls 3, and the second steel plate...
PUM
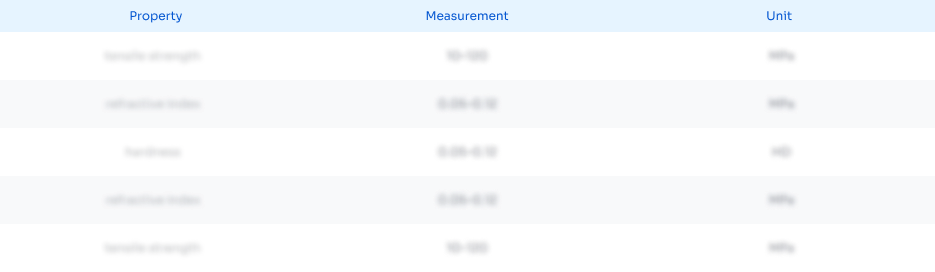
Abstract
Description
Claims
Application Information

- Generate Ideas
- Intellectual Property
- Life Sciences
- Materials
- Tech Scout
- Unparalleled Data Quality
- Higher Quality Content
- 60% Fewer Hallucinations
Browse by: Latest US Patents, China's latest patents, Technical Efficacy Thesaurus, Application Domain, Technology Topic, Popular Technical Reports.
© 2025 PatSnap. All rights reserved.Legal|Privacy policy|Modern Slavery Act Transparency Statement|Sitemap|About US| Contact US: help@patsnap.com