Fluid director using exhaust leaving velocity loss of steam turbine
A residual speed loss, steam turbine technology, applied in the direction of machines/engines, components of pumping devices for elastic fluids, mechanical equipment, etc., can solve the problems of increasing the length of the main shaft of the steam turbine, affecting the efficiency of the low-pressure cylinder, and lack of feasibility. , to achieve the effect of reduced heat consumption rate, significant energy saving benefits, and easy implementation
- Summary
- Abstract
- Description
- Claims
- Application Information
AI Technical Summary
Problems solved by technology
Method used
Image
Examples
Embodiment Construction
[0014] In order to make the purpose, technical solution and advantages of the present invention more clear and concise, the present invention will be further described in detail below in conjunction with the accompanying drawings and embodiments. It should be understood that the specific embodiments described here are only used to explain the present invention, not to limit the present invention.
[0015] Such as figure 1 middle figure 1 a and figure 1 As shown in b, the present invention is a deflector utilizing steam turbine exhaust after-velocity loss. The deflector 1 is arranged downstream of the last-stage moving blade 2 of the steam turbine and fixed on the cylinder 3 of the steam turbine. The deflector 1 It consists of a plurality of S-shaped annular deflectors 5 socketed. Adjacent annular deflectors 5 are fixed radially by multiple fixers 6 with streamlined cross-sections. Adjacent annular deflectors 5 forms diversion passage 4; The direction of the entrance of said...
PUM
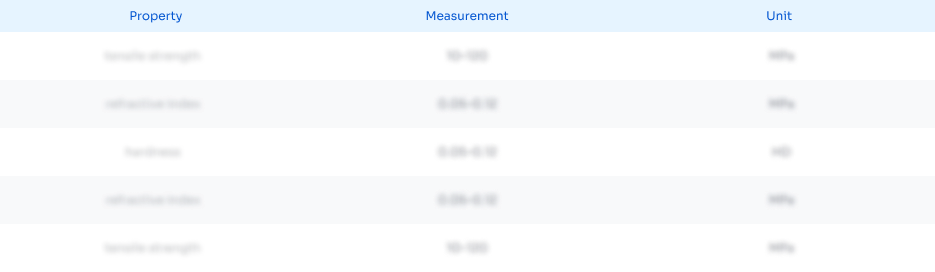
Abstract
Description
Claims
Application Information

- R&D
- Intellectual Property
- Life Sciences
- Materials
- Tech Scout
- Unparalleled Data Quality
- Higher Quality Content
- 60% Fewer Hallucinations
Browse by: Latest US Patents, China's latest patents, Technical Efficacy Thesaurus, Application Domain, Technology Topic, Popular Technical Reports.
© 2025 PatSnap. All rights reserved.Legal|Privacy policy|Modern Slavery Act Transparency Statement|Sitemap|About US| Contact US: help@patsnap.com