A tire rubber pyrolysis method combined with pyrolysis gas circulation heating and microwave
A technology of circulating heating and cracking gas, which is applied in special forms of carbonization, coking ovens, petroleum industry, etc., can solve the problems of cracking products not meeting environmental protection requirements, low controllability of cracking treatment process, low cracking efficiency, etc. Utilization efficiency, improvement of microwave absorption capacity, and effect of increasing cracking efficiency
- Summary
- Abstract
- Description
- Claims
- Application Information
AI Technical Summary
Problems solved by technology
Method used
Image
Examples
Embodiment 1
[0040] A tire rubber cracking method combined with pyrolysis gas circulation heating and microwave, said method comprises the following steps:
[0041] A. Tire rubber pretreatment; mainly to clean the tire rubber and then break it into 25cm 2 left and right small pieces;
[0042] B, the tire rubber pretreated in step A is sent into the composite cracking chamber;
[0043] C. Use a gas heating device to heat the gas medium to 350°C;
[0044] D, the gas heated in step C is continuously fed into the composite cracking chamber and the microwave acts on the tire rubber simultaneously for cracking to obtain a solid product and a mixed gaseous product;
[0045] E, the mixed gaseous product that step D obtains carries out oil-gas separation and removes cracking oil;
[0046] F. Part of the gas obtained through oil and gas separation in step E is passed into the gas heating device described in step C and heated to 350 ° C for step D cyclic cracking, and the rest is discharged, and t...
Embodiment 2
[0048] A tire rubber cracking method combined with pyrolysis gas circulation heating and microwave, said method comprises the following steps:
[0049] A. Tire rubber pretreatment; mainly to clean the tire rubber and then break it into 25cm 2 left and right small pieces;
[0050] B, the tire rubber pretreated in step A is sent into the composite cracking chamber;
[0051] C. Use a gas heating device to heat the gas medium to 700°C; the gas medium is an inert gas;
[0052] D, the gas heated in step C is continuously fed into the composite cracking chamber and the microwave acts on the tire rubber simultaneously for cracking to obtain a solid product and a mixed gaseous product;
[0053] E, the mixed gaseous product that step D obtains carries out oil-gas separation and removes cracking oil;
[0054] F. Pass the part of the gas obtained through oil and gas separation in step E into the gas heating device described in step C and heat it to 700 ° C for step D cyclic cracking, a...
Embodiment 3
[0056] A tire rubber cracking method combined with pyrolysis gas circulation heating and microwave, said method comprises the following steps:
[0057] A. Tire rubber pretreatment; mainly to clean the tire rubber and then break it into 25cm 2 left and right small pieces;
[0058] B, the tire rubber pretreated in step A is sent into the composite cracking chamber;
[0059] C. Use a gas heating device to heat the gas medium to 450°C; the gas medium is water vapor;
[0060] D, the gas heated in step C is continuously fed into the composite cracking chamber and the microwave acts on the tire rubber simultaneously for cracking to obtain solid products and mixed gaseous products; the microwave frequency of cracking is 2450MHz ± 50MHz;
[0061] E, the mixed gaseous product that step D obtains carries out oil-gas separation and removes cracking oil;
[0062] F. Part of the gas obtained through oil and gas separation in step E is passed into the gas heating device described in step ...
PUM
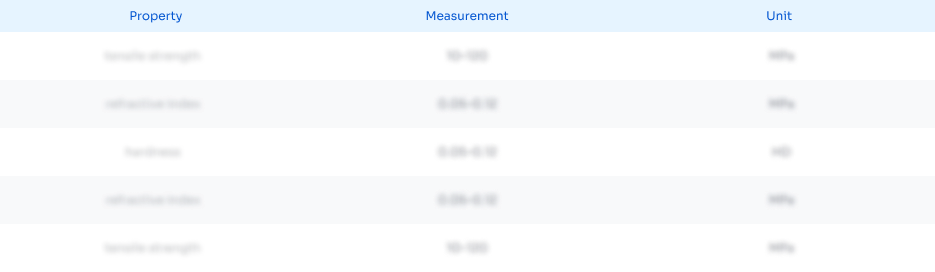
Abstract
Description
Claims
Application Information

- R&D
- Intellectual Property
- Life Sciences
- Materials
- Tech Scout
- Unparalleled Data Quality
- Higher Quality Content
- 60% Fewer Hallucinations
Browse by: Latest US Patents, China's latest patents, Technical Efficacy Thesaurus, Application Domain, Technology Topic, Popular Technical Reports.
© 2025 PatSnap. All rights reserved.Legal|Privacy policy|Modern Slavery Act Transparency Statement|Sitemap|About US| Contact US: help@patsnap.com