Biomass particle forming mechanism with spiral groove press rollers
A technology of spiral grooves and forming mechanisms, which is applied in the direction of material forming presses, presses, manufacturing tools, etc., can solve the problems of limited feeding space, great influence on particle forming, and slipping of pressure rollers, so as to reduce manufacturing and Maintenance cost, improvement of compression force, effect of increasing material compression chamber
- Summary
- Abstract
- Description
- Claims
- Application Information
AI Technical Summary
Problems solved by technology
Method used
Image
Examples
Embodiment Construction
[0023] See figure 1 , 2 , the concrete structure is as follows: the present invention is provided with upper frame 5 and lower frame 3, and upper and lower ends of upper frame 5 are respectively fixed and assembled forming mold upper cover plate 8, forming mold lower cover plate 11; 8 and the lower cover plate 11 of the forming mold are provided with a compression cavity, and the compression cavity is composed of the upper cover plate 8 of the forming cavity, the upper support bearing 13, the ring die 4, the outer ring toothed bearing 10, the lower cover plate 11 of the forming mold, etc. A closed cavity formed by parts. The inner ring of the upper support bearing 13 and the upper cover plate 8 of the molding cavity are fastened and connected by bolts, and the outer ring of the upper support bearing 13 is also connected with the upper end surface of the ring die 4 by bolts; The ring gear end face of the ring toothed bearing 10 is connected, and the inner ring of the outer ri...
PUM
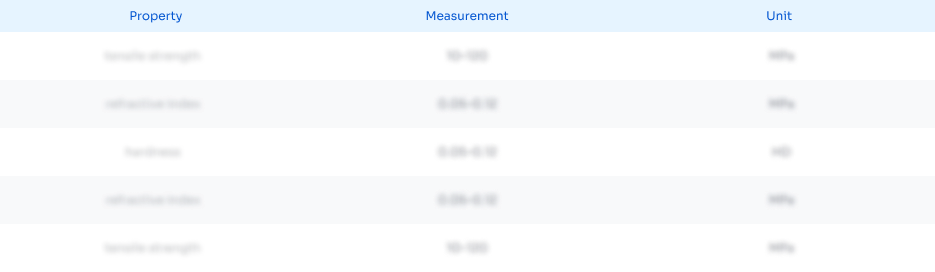
Abstract
Description
Claims
Application Information

- R&D
- Intellectual Property
- Life Sciences
- Materials
- Tech Scout
- Unparalleled Data Quality
- Higher Quality Content
- 60% Fewer Hallucinations
Browse by: Latest US Patents, China's latest patents, Technical Efficacy Thesaurus, Application Domain, Technology Topic, Popular Technical Reports.
© 2025 PatSnap. All rights reserved.Legal|Privacy policy|Modern Slavery Act Transparency Statement|Sitemap|About US| Contact US: help@patsnap.com