A micro-packed bed bionic reactor
A technology of biomimetic reactor and packed bed, applied in the direction of chemical instruments and methods, chemical/physical processes, etc., can solve the problems of complex catalyst chip preparation process, difficulty in ensuring mechanical strength, difficulty in large-scale industrial application, etc., and achieve reaction retention The effect of constant time, uniform distribution of reaction load, and low cost
- Summary
- Abstract
- Description
- Claims
- Application Information
AI Technical Summary
Problems solved by technology
Method used
Image
Examples
Embodiment 1
[0032] The ammonia synthesis reaction is a typical fast gas-solid catalyst reaction. The traditional process uses iron-based catalysts, but the use of ruthenium-based catalysts with better catalytic performance can significantly increase the yield of ammonia synthesis reactions and reduce the reaction pressure from 150-200MPa to 100- 150MPa, which has greatly improved the reduction of energy consumption and stable operation process. Nevertheless, the ammonia synthesis reactor still uses a traditional fixed-bed reactor, and the single-pass pressure drop is as high as 2-3 atm under the operating pressure of 100 MPa, and the energy consumption of the ammonia synthesis reaction process is too high due to the large amount of reaction gas circulating at a high space velocity.
[0033] In this example, a micro-packed bed biomimetic reactor with a single-channel arterial structure is applied to the synthesis of ammonia with a ruthenium-based catalyst to evaluate its performance.
[00...
Embodiment 2
[0044] The carbon monoxide water-gas shift reaction is a fast gas-solid catalytic reaction. At present, large-particle catalysts and traditional fixed-bed reactors are mainly used in industry. The micro-packed bed bionic reactor with three-channel arterial structure in this example is applied to the carbon monoxide low-temperature shift reaction. , to evaluate its performance.
[0045] The overall appearance, top sectional view and front sectional view of the micro-packed bed biomimetic reactor with three-channel arterial structure are shown in Figure 3(a), Figure 3(b) and Figure 3(c), and the catalyst filling method is " Parallel fill" type. The gas flow direction in the reactor structural unit is that the cold raw material gas flows in from port 301, flows to the bottom of the intake channel, rebounds to the top through the rebound channel 302 with metal heat conducting rods 303 inserted on both sides, and passes through the cordierite on both sides during the rebound proces...
Embodiment 3
[0056] A large amount of coal bed gas (also known as gas) is produced in the process of coal mining, and its main component is methane. Currently, gas utilization technologies with a methane concentration greater than 30% are basically mature, while low-concentration gas is difficult to burn and utilize under normal conditions due to its low concentration. At present, the industry mainly adopts regenerative flow-direction conversion catalytic combustion fixed-bed reactors filled with large-particle catalysts. The utilization rate of catalysts is low and the operating conditions of the reactors are unstable. Applied to the carbon monoxide shift reaction to evaluate its performance.
[0057] Figure 4(a) and Figure 4(b) show the overall appearance and top section of the micro-packed bed biomimetic reactor with three-channel arterial structure. The catalyst filling method is "vertical filling" type, and the reactor structure is viewed from above, The side view, rear view and fron...
PUM
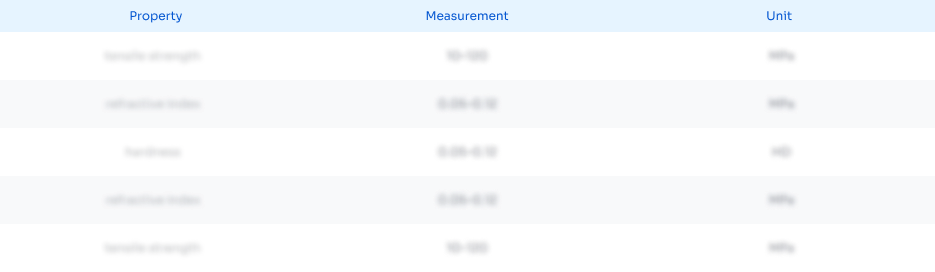
Abstract
Description
Claims
Application Information

- Generate Ideas
- Intellectual Property
- Life Sciences
- Materials
- Tech Scout
- Unparalleled Data Quality
- Higher Quality Content
- 60% Fewer Hallucinations
Browse by: Latest US Patents, China's latest patents, Technical Efficacy Thesaurus, Application Domain, Technology Topic, Popular Technical Reports.
© 2025 PatSnap. All rights reserved.Legal|Privacy policy|Modern Slavery Act Transparency Statement|Sitemap|About US| Contact US: help@patsnap.com