Printing and dyeing production process for pure cotton fabric
A pure cotton fabric, printing and dyeing technology, applied in the field of textile production, can solve problems such as high energy consumption and complexity, and achieve the effects of improving production efficiency, increasing cycle time, and reducing processes
- Summary
- Abstract
- Description
- Claims
- Application Information
AI Technical Summary
Problems solved by technology
Method used
Examples
Embodiment 1
[0020] A printing and dyeing production process for pure cotton fabrics, comprising the following steps:
[0021] 1) Pretreatment of fabric
[0022] The pure cotton fabric is turned over, singeing, and rolled, and stacked in a steam box at 30°C for 90 minutes, then washed and dried, and desizing is carried out under the condition of stacking in a steam box at 30°C for 90 minutes;
[0023] 2) Dyeing
[0024] Dip the pre-treated fabric into the dyeing tank for dyeing, control the bath ratio in the dyeing tank to 1:12, dip-dye at 25°C for 8 minutes, then heat up to 50°C and dip-dye for 15 minutes; the dyeing solution in the dyeing tank contains the following components: dye 15g / L, N-methylolacrylamide 5g / L, methylene diphenyl ether disulfonate 5g / L, polyquaternium color fixing agent 2g / L, water glass 5g / L, dimethyl dihydroxy Cycloethylene urea resin 2g / L, isopropanol 0.6g / L, sodium naphthalene ethylene sulfate 0.05g / L, diethylenetriaminepentaacetic acid 0.35g / L, wet rubbing fas...
Embodiment 2
[0031] A printing and dyeing production process for pure cotton fabrics, comprising the following steps:
[0032] 1) Pretreatment of fabric
[0033] The pure cotton fabric is turned over, singeing, and rolled, and stacked in a steamer at 40°C for 100 minutes, then washed and dried, and desizing is carried out under the condition of stacking in a steamer at 40°C for 100 minutes;
[0034] 2) Dyeing
[0035] Dip the pre-treated fabric into the dyeing tank for dyeing, control the bath ratio in the dyeing tank to 1:15, dip-dye at 30°C for 10 minutes, then heat up to 60°C and dip-dye for 20 minutes; the dyeing solution in the dyeing tank contains the following components: dye 20g / L, N-methylolacrylamide 8g / L, methylene diphenyl ether disulfonate 7g / L, polyquaternium color fixing agent 4g / L, water glass 10g / L, dimethyl dihydroxy Cycloethylene urea resin 5g / L, isopropanol 0.8g / L, sodium naphthalene ethylene sulfate 0.25g / L, diethylenetriaminepentaacetic acid 0.55g / L, wet rubbing fas...
Embodiment 3
[0042] A printing and dyeing production process for pure cotton fabrics, comprising the following steps:
[0043] 1) Pretreatment of fabric
[0044] The pure cotton fabric is turned over, singeing, and rolled, and stacked in a steam box at 35°C for 95 minutes, then washed and dried, and desizing is carried out under the condition of stacking in a steam box at 35°C for 95 minutes;
[0045] 2) Dyeing
[0046]Dip the pre-treated fabric into the dyeing tank for dyeing, control the bath ratio in the dyeing tank to 1:13, dip-dye at 27°C for 9 minutes, then heat up to 55°C and dip-dye for 17 minutes; the dyeing solution in the dyeing tank contains the following components: dye 17g / L, N-methylolacrylamide 7g / L, methylene diphenyl ether disulfonate 6g / L, polyquaternium color fixing agent 3g / L, water glass 8g / L, dimethyl dihydroxy Cycloethylene urea resin 4g / L, isopropanol 0.7g / L, sodium naphthalene ethylene sulfate 0.15g / L, diethylenetriaminepentaacetic acid 0.45g / L, wet rubbing fast...
PUM
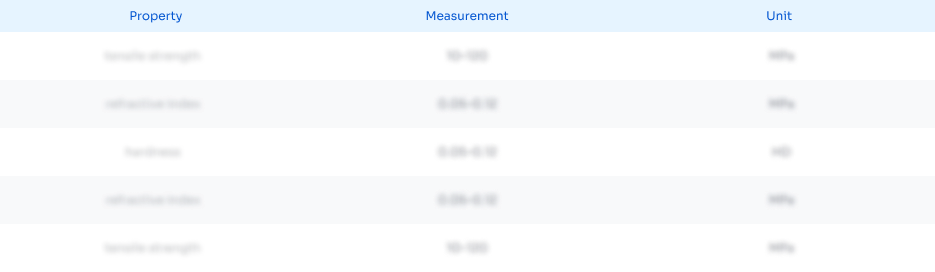
Abstract
Description
Claims
Application Information

- R&D Engineer
- R&D Manager
- IP Professional
- Industry Leading Data Capabilities
- Powerful AI technology
- Patent DNA Extraction
Browse by: Latest US Patents, China's latest patents, Technical Efficacy Thesaurus, Application Domain, Technology Topic, Popular Technical Reports.
© 2024 PatSnap. All rights reserved.Legal|Privacy policy|Modern Slavery Act Transparency Statement|Sitemap|About US| Contact US: help@patsnap.com