A kind of matt elastic thermal transfer film and preparation method thereof
A technology of thermal transfer and elastic force, applied in the direction of temperature recording method, coating, polyurea/polyurethane coating, etc., can solve the problem that it is difficult to meet the dullness at the same time, achieve high dullness and friction resistance, improve grades, and improve durability The effect of friction properties
- Summary
- Abstract
- Description
- Claims
- Application Information
AI Technical Summary
Problems solved by technology
Method used
Image
Examples
Embodiment 1
[0029] Embodiment 1 of a preparation method of a matt elastic thermal transfer film: a preparation method of a matt elastic thermal transfer film, the preparation steps are as follows
[0030] 1) Use biaxially stretched polyester film as the base film, hereinafter referred to as PET base film;
[0031] 2) Coating on the surface of the PET base film to form a matt pre-coat: mix 57.5% of acrylic modified silicone resin and 40% of cyclohexanone and stir for 20min, then add 2.5% of the accelerator of the above mixed solution and mix Uniformly made matte pre-coating liquid. The material is coated on the surface of PET polyester film through a coating machine, and then reacted and dried in a 4-stage high-temperature oven to form a matte pre-coating layer; the matte pre-coating layer can make the glossy PET base film appear Matte, after transfer printing, it can make the substrate have a matte effect, and at the same time make it scratch-resistant and wear-resistant.
[0032] 3) Mi...
Embodiment 2
[0036] Example 2 of a preparation method of a matt elastic heat transfer film: a preparation method of a matt elastic heat transfer film, the preparation steps are as follows
[0037] 1) Use biaxially stretched polyester film as the base film, hereinafter referred to as PET base film;
[0038] 2) Coating on the surface of the PET base film to form a matt pre-coat: 65% of acrylic modified silicone resin, 22% of butyl ester, and 10% of cyclohexanone were mixed and stirred for 25 minutes, and then added to the above mixed solution 3% accelerator is mixed evenly to make matte pre-coating liquid. The material is coated on the surface of PET polyester film through a coating machine, and then reacted and dried in a 5-stage high-temperature oven to form a matte pre-coating layer; the matte pre-coating layer can make the glossy PET base film appear Matte, after transfer printing, it can make the substrate have a matte effect, and at the same time make it scratch-resistant and wear-res...
PUM
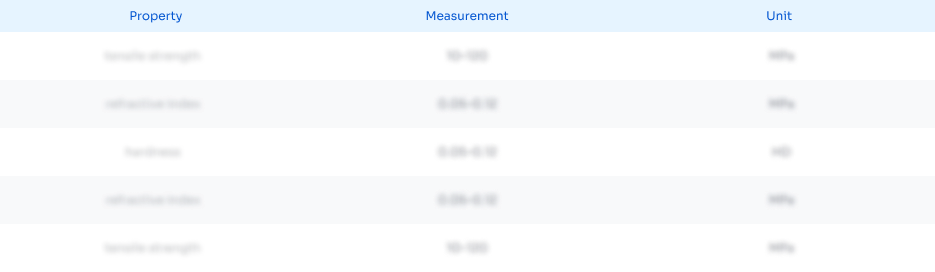
Abstract
Description
Claims
Application Information

- R&D Engineer
- R&D Manager
- IP Professional
- Industry Leading Data Capabilities
- Powerful AI technology
- Patent DNA Extraction
Browse by: Latest US Patents, China's latest patents, Technical Efficacy Thesaurus, Application Domain, Technology Topic, Popular Technical Reports.
© 2024 PatSnap. All rights reserved.Legal|Privacy policy|Modern Slavery Act Transparency Statement|Sitemap|About US| Contact US: help@patsnap.com