Casting welding line polishing paste
A technique for polishing paste and castings, which is applied in the direction of polishing compositions, polishing compositions containing abrasives, chemical instruments and methods, etc. It can solve the problems of easily damaged welds and failure to meet the use requirements, etc., so as to improve the polishing accuracy, Improving the surface quality of castings and the effect of suitable viscosity
- Summary
- Abstract
- Description
- Claims
- Application Information
AI Technical Summary
Problems solved by technology
Method used
Examples
Embodiment 1
[0015] (1) 6 parts of wax additives are added to 50 parts of paraffin oil, and then 5 parts of chlorinated paraffin and 4 parts of cis-butadiene rubber are added after uniform dispersion, and then heated to 80-90 ℃ of insulation and mixing for 15min to obtain material I;
[0016] (2) Fully mix 25 parts of alumina powder, 10 parts of nano-ceramic powder and 6 parts of sepiolite powder, dry at 100-110 ℃ for 12 hours, and then calcine at 350-400 ℃ for 3 hours to obtain material II;
[0017] (3) Add material II, 8 parts of activated clay, 8 parts of hydrogenated castor oil, 3 parts of polyvinyl chloride resin, 3 parts of polyacrylamide, 2 parts of sodium petroleum sulfonate and 2 parts of barium stearate to material I, fully Mix well.
[0018] Preparation of wax additives: firstly, 15 parts of carnauba wax and 10 parts of microcrystalline wax were mixed and heated until completely melted, then 5 parts of carboxy resin, 1 part of styrene-butadiene rubber and 10 parts of glycerol we...
Embodiment 2
[0020] (1) 10 parts of wax additives are added to 60 parts of paraffin oil, 8 parts of chlorinated paraffins and 4 parts of cis-butadiene rubber are added after dispersing evenly, then heated to 80-90 ℃ of insulation mixing for 15min, to obtain material I;
[0021] (2) Fully mix 30 parts of alumina powder, 12 parts of nano-ceramic powder and 5 parts of sepiolite powder, put it at 100-110 ℃ to dry for 12 hours, and then calcine it at 350-400 ℃ for 3 hours to obtain material II;
[0022] (3) add material II, 10 parts of activated clay, 6 parts of hydrogenated castor oil, 5 parts of polyvinyl chloride resin, 4 parts of polyacrylamide, 3 parts of sodium petroleum sulfonate and 1 part of barium stearate to material I, fully Mix well.
[0023] Preparation of wax additives: firstly, 20 parts of carnauba wax and 15 parts of microcrystalline wax were mixed and heated until completely melted, then 6 parts of carbomer resin, 2 parts of styrene-butadiene rubber and 15 parts of glycerol we...
PUM
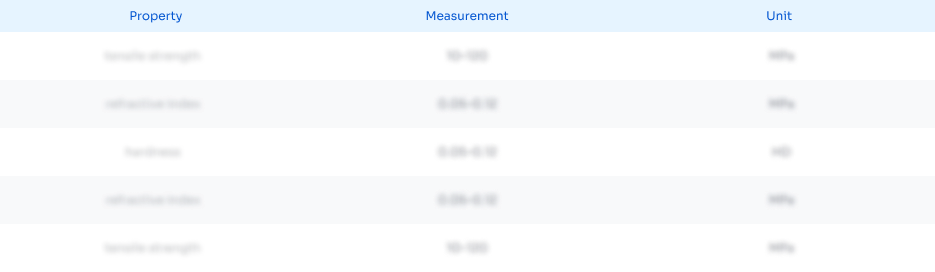
Abstract
Description
Claims
Application Information

- R&D
- Intellectual Property
- Life Sciences
- Materials
- Tech Scout
- Unparalleled Data Quality
- Higher Quality Content
- 60% Fewer Hallucinations
Browse by: Latest US Patents, China's latest patents, Technical Efficacy Thesaurus, Application Domain, Technology Topic, Popular Technical Reports.
© 2025 PatSnap. All rights reserved.Legal|Privacy policy|Modern Slavery Act Transparency Statement|Sitemap|About US| Contact US: help@patsnap.com