A detector landing buffer mechanism
A buffer mechanism and detector technology, which is applied in the directions of aerospace vehicle landing devices, aircraft, motor vehicles, etc., can solve the problems of enlarged radial size and complex structure of auxiliary struts, achieve reasonable energy absorption, and reduce the workload of assembly , buffering and reliable effect
- Summary
- Abstract
- Description
- Claims
- Application Information
AI Technical Summary
Problems solved by technology
Method used
Image
Examples
Embodiment Construction
[0020] like figure 2 As shown, it is a landing buffer mechanism in a folded, compressed and folded state, which includes a main pillar 5, a multifunctional auxiliary pillar 4, a single-function auxiliary pillar 6 and a foot pad 10, and the two ends of the main pillar 5 pass through the first universal joint respectively. 2 and the first ball pair 9 are connected with the detector and the foot pad 10, and the two ends of the multifunctional auxiliary pillar 4 are respectively connected with the detector and the main pillar 5 through the second universal joint 1 and the second ball pair 7, and the single-function auxiliary The two ends of the pillar 6 are respectively connected to the detector and the main pillar 5 through the third universal joint 3 and the third ball pair 8. The main pillar 5 is a piston structure, and its interior is equipped with anti-compression impact material, which is mainly used to cushion the landing. longitudinal impact load. The multifunctional aux...
PUM
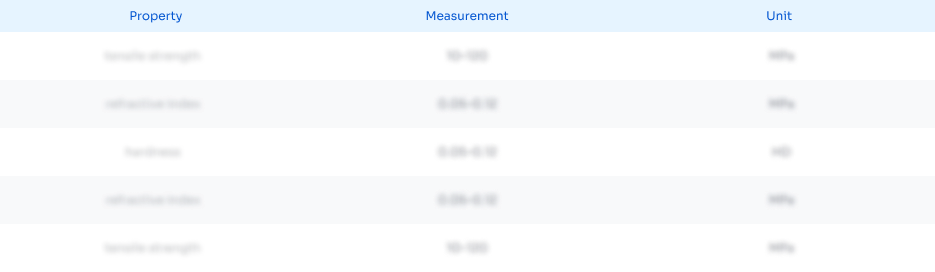
Abstract
Description
Claims
Application Information

- R&D Engineer
- R&D Manager
- IP Professional
- Industry Leading Data Capabilities
- Powerful AI technology
- Patent DNA Extraction
Browse by: Latest US Patents, China's latest patents, Technical Efficacy Thesaurus, Application Domain, Technology Topic, Popular Technical Reports.
© 2024 PatSnap. All rights reserved.Legal|Privacy policy|Modern Slavery Act Transparency Statement|Sitemap|About US| Contact US: help@patsnap.com