Sulfur-tolerant shift reaction equipment and sulfur-tolerant shift process method
A technology of sulfur-resistant conversion and reaction equipment, which is applied in chemical instruments and methods, inorganic chemistry, non-metallic elements, etc., can solve the problems of inability to tolerate sulfur-CO conversion, and achieve the effect of inhibiting agglomeration
- Summary
- Abstract
- Description
- Claims
- Application Information
AI Technical Summary
Problems solved by technology
Method used
Image
Examples
Embodiment 1
[0038] This embodiment provides a sulfur-resistant shift reaction equipment, such as figure 1 As shown, it includes a first-stage shift reactor 1, a second-stage shift reactor 2, and a third-stage shift reactor 3 connected in series; wherein, the first-stage shift reactor 1 is filled with MgAl 2 o 4 As the carrier, CoO and MoO 3 is the catalyst of the main active component; the second stage shift reactor 2 is filled with MgAl 2 o 4 As the carrier, CoO and MoO 3 As the main active component, the catalyst with rare earth oxide as active promoter; the third stage shift reactor 3 is filled with MgAl 2 o 4 or Al 2 o 3 As the carrier, CoO and MoO 3 as the main active component, with K 2 O is the catalyst of the coagent.
[0039] In the sulfur-resistant shift reaction equipment provided in this embodiment, the first-stage shift reactor 1 is filled with MgAl 2 o 4 As the carrier, CoO and MoO 3 As the main active component of the catalyst, the catalyst has low sulfur resis...
Embodiment 2
[0054] This embodiment provides a sulfur-tolerant shift process, which includes the following steps: feed the raw material gas into the first-stage shift reactor 1 for shift reaction, and the first-stage shift reactor 1 is filled with MgAl 2 o 4 As the carrier, CoO and MoO 3 Catalyst that is the main active component; the shift gas from the first-stage shift reactor 1 is passed into the second-stage shift reactor 2 for shift reaction, and the second-stage shift reactor 2 is filled with MgAl 2 o 4 As the carrier, CoO and MoO 3 as the main active component, a catalyst with rare earth oxides as active promoters; the shift gas from the second-stage shift reactor 2 is passed into the third-stage shift reactor 3 for shift reaction, and the third-stage shift Reactor 3 was filled with MgAl 2 o 4 or Al 2 o 3 As the carrier, CoO and MoO 3 as the main active component, with K 2 O is the catalyst of the coagent.
[0055] In the sulfur-resistant shift process method provided in t...
PUM
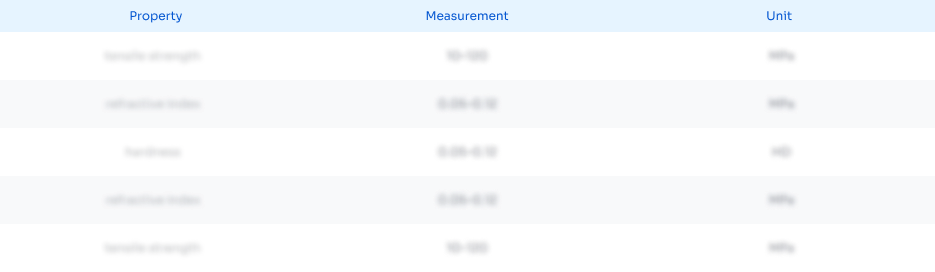
Abstract
Description
Claims
Application Information

- Generate Ideas
- Intellectual Property
- Life Sciences
- Materials
- Tech Scout
- Unparalleled Data Quality
- Higher Quality Content
- 60% Fewer Hallucinations
Browse by: Latest US Patents, China's latest patents, Technical Efficacy Thesaurus, Application Domain, Technology Topic, Popular Technical Reports.
© 2025 PatSnap. All rights reserved.Legal|Privacy policy|Modern Slavery Act Transparency Statement|Sitemap|About US| Contact US: help@patsnap.com