A method for improving the hot-damp resistance of CEM-1 copper-clad laminates
A technology of copper clad laminate and CEM-1, applied in the field of copper clad laminate, can solve the problem that copper clad laminate cannot be guaranteed the heat resistance of copper clad laminate, so as to reduce the risk of foaming and delamination and enhance chemical effect strength, and the effect of enhancing other properties
- Summary
- Abstract
- Description
- Claims
- Application Information
AI Technical Summary
Problems solved by technology
Method used
Image
Examples
preparation example Construction
[0052] The preparation method of embodiment copper-clad laminate:
[0053] 1) Preparation of water-soluble small molecule resin composition
[0054] Put the water-soluble phenolic resin, water-soluble cyclotriphosphazene flame retardant, water-soluble nitrogen-containing flame retardant, and additives into the container, stir to make them evenly mixed, and adjust the solid content of the solution to 15% to 30% with a solvent. Make glue solution, promptly obtain water-soluble small molecule resin composition.
[0055] 2) Preparation of oil-soluble small molecule resin composition
[0056] The phosphorus-containing epoxy resin and the phosphazene resin are put into a container, stirred to make them evenly mixed, and the solid content of the solution is adjusted to 15% with a solvent to make a glue solution, and the oil-soluble small molecule resin composition is obtained.
[0057] 3) Preparation of oil-soluble macromolecular resin composition
[0058] Put phosphorus-containin...
Embodiment 1
[0095] Comparing Example 1 with Comparative Example 1, Comparative Example 2, and Comparative Example 3, it can be seen that Comparative Example 1 is superior to Example 1 in terms of dipping solderability, 240°C baking plate, and T260, but its moisture resistance is not as good as that of Example 1, and there is no Flame retardancy, indicating that simply using water-soluble phenolic resin can greatly improve the heat resistance of copper clad laminates, but copper clad laminates are not flame retardant. Although the flame retardancy of Comparative Example 2 is improved compared with Comparative Example 1, it still does not reach the V-0 level, and the heat resistance also reduces to some extent simultaneously, and its comprehensive performance is not as good as that of Example 1, indicating that the introduction of cyclotriphosphazene Flame retardants can improve the flame retardancy of copper clad laminates, and have no major impact on heat resistance. Compared with Example...
PUM
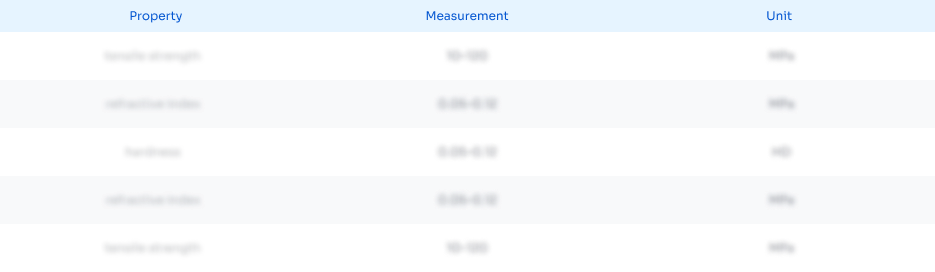
Abstract
Description
Claims
Application Information

- R&D Engineer
- R&D Manager
- IP Professional
- Industry Leading Data Capabilities
- Powerful AI technology
- Patent DNA Extraction
Browse by: Latest US Patents, China's latest patents, Technical Efficacy Thesaurus, Application Domain, Technology Topic, Popular Technical Reports.
© 2024 PatSnap. All rights reserved.Legal|Privacy policy|Modern Slavery Act Transparency Statement|Sitemap|About US| Contact US: help@patsnap.com