Combustor for gas turbine and flame combustion method
A gas turbine and burner technology, which is applied in the direction of combustion methods, combustion chambers, combustion equipment, etc., can solve the problems of combustion stability tempering, combustion instability, and low pollution emissions, and achieve strong combustion stability and enhanced combustion stability , Low NOx emission effect
- Summary
- Abstract
- Description
- Claims
- Application Information
AI Technical Summary
Problems solved by technology
Method used
Image
Examples
Embodiment 1
[0049] Such as figure 1 As shown, the burner for the gas turbine in this embodiment includes a connected central duty burner 100 and a main premix burner 200;
[0050] The central duty burner 100 includes a duty burner body 110; the air inlet 111 of the duty burner body 110 is provided with a central duty nozzle 120; Communicating with the main premix burner 200, the inner wall of the flame control pipe 130 is an inwardly convex arc structure;
[0051]A concave cavity 140 is provided along the circumference of the inner wall of the duty burner body 110. The concave cavity 140 is a circular structure. Along the central axis of the duty burner body 110, the concave cavity 140 is located between the central duty nozzle 120 and the flame control pipe. Between 130, the concave cavity 140 is provided with a cavity fuel port and a cavity air inlet 141;
[0052] The inside of the duty burner body 110 is also provided with a central blunt body 150. Along the central axis direction of...
Embodiment 2
[0060] Such as figure 2 and image 3 As shown, the difference between this embodiment and Embodiment 1 is that the cavity fuel port and the cavity air inlet 141 are both arranged on the side of the cavity 140 close to the flame control pipe 130, that is, the rear edge of the cavity 140, The equivalence ratio of fuel to air in cavity 140 is the actual fuel to air ratio divided by the fuel to air ratio for complete combustion; the equivalence ratio of fuel to air in cavity 140 is 1.2 to 1.4; the actual fuel to air ratio is the cavity of cavity 140 The ratio of the fuel mass actually passed into the body fuel port and the air mass actually passed into the cavity air inlet 141; the fuel-air ratio of complete combustion is when the winding material is fully burned, the quality of the fuel used and the required The ratio of the mass of air. This ratio ensures that a rich fuel is formed in the cavity 140 . The fuel is introduced from the fuel ring pipe arranged on the concave cav...
PUM
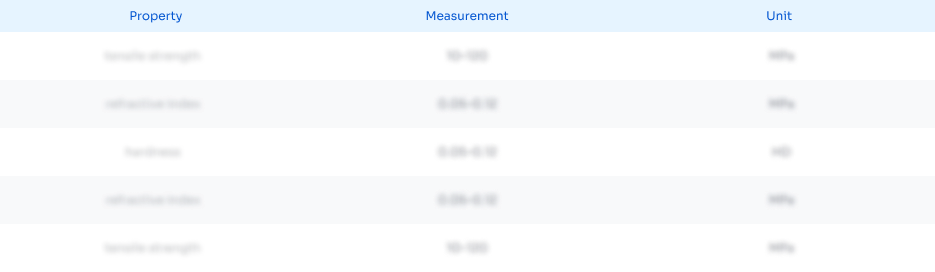
Abstract
Description
Claims
Application Information

- R&D
- Intellectual Property
- Life Sciences
- Materials
- Tech Scout
- Unparalleled Data Quality
- Higher Quality Content
- 60% Fewer Hallucinations
Browse by: Latest US Patents, China's latest patents, Technical Efficacy Thesaurus, Application Domain, Technology Topic, Popular Technical Reports.
© 2025 PatSnap. All rights reserved.Legal|Privacy policy|Modern Slavery Act Transparency Statement|Sitemap|About US| Contact US: help@patsnap.com