Method for one-step forming of microcrystal glass plate through molten-state blast furnace slag
A technology of glass-ceramics and blast furnace slag, which is applied in glass molding, glass manufacturing equipment, manufacturing tools, etc., can solve the problems of large energy consumption, high production cost, and complicated process, so as to avoid energy waste, reduce production cost and Manufacturing cycle and the effect of simplifying the preparation steps
- Summary
- Abstract
- Description
- Claims
- Application Information
AI Technical Summary
Problems solved by technology
Method used
Image
Examples
Embodiment 1
[0030] (1) The amount of blast furnace slag is designed to be 37%, and the target composition (wt.%) of blast furnace slag glass ceramics is: CaO15%, SiO 2 50%, Al 2 o 3 12%, MgO10%, K 2 O3%, ZnO3%, TiO 2 5%, other components in blast furnace slag are ignored.
[0031] (2) The test results of the chemical composition of the blast furnace slag from the previous heat were CaO40.57%, SiO 2 34.15%, Al 2 o 3 15.88%, MgO7.88%, K 2 O0.57%, TiO 2 0.95%, the test result of this composition represents the chemical composition of the liquid blast furnace slag used this time. The liquid blast furnace slag used in the implementation of this example is 370g. After calculation, the required amounts of various auxiliary materials are: SiO 2 374g, Al 2 o 3 61g, MgO71g, K 2 O27g, TiO 2 46g, ZnO30g, these auxiliary materials are mixed, and together with the liquid blast furnace slag, they are quickly inserted into the constant temperature graphite crucible in batches. The graphite ...
Embodiment 2
[0035] (1) The amount of blast furnace slag is designed to be 61.6%, and the target composition (wt.%) of blast furnace slag glass ceramics is: CaO25%, SiO 2 40%, Al 2 o 3 12%, MgO10%, K 2 O3%, ZnO3%, TiO 2 5%, other components in blast furnace slag are ignored.
[0036] (2) The test results of the chemical composition of the blast furnace slag from the previous heat were CaO40.57%, SiO 2 34.15%, Al 2 o 3 15.88%, MgO7.88%, K 2 O0.57%, TiO 2 0.95%, the test result of this composition represents the chemical composition of the liquid blast furnace slag used this time. The amount of liquid blast furnace slag used in the implementation of this example is 616g. After calculation, the required amounts of various auxiliary materials are: SiO 2 190g, Al 2 o 3 22g, MgO52g, K 2 O26g, TiO 2 44g, ZnO30g, these auxiliary materials are mixed, and together with the liquid blast furnace slag, they are quickly inserted into the constant temperature graphite crucible in batches. T...
Embodiment 3
[0040] (1) The amount of blast furnace slag is designed to be 37%, and the target composition (wt.%) of blast furnace slag glass ceramics is: CaO15%, SiO 2 50%, Al 2 o 3 12%, MgO10%, K 2 O3%, ZnO3%, TiO 2 5%, other components in blast furnace slag are ignored.
[0041] (2) The test results of the chemical composition of the blast furnace slag from the previous heat were CaO40.57%, SiO 2 34.15%, Al 2 o 3 15.88%, MgO7.88%, K 2 O0.57%, TiO 2 0.95%, the test result of this composition represents the chemical composition of the liquid blast furnace slag used this time. The liquid blast furnace slag used in the implementation of this example is 370g. After calculation, the required amounts of various auxiliary materials are: SiO 2 374g, Al 2 o 3 61g, MgO71g, K 2 O27g, TiO 2 46g, ZnO30g, these auxiliary materials are mixed, and together with the liquid blast furnace slag, they are quickly inserted into the constant temperature graphite crucible in batches. The graphite ...
PUM
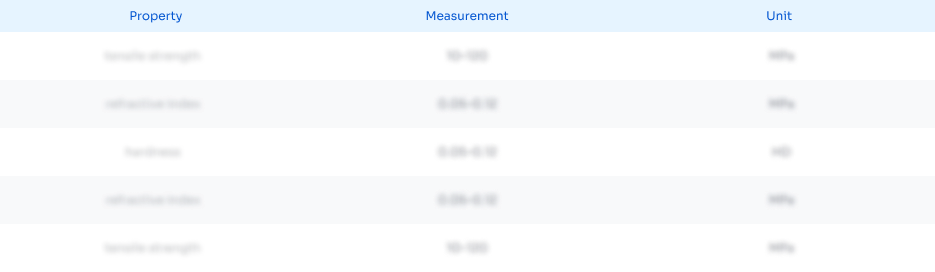
Abstract
Description
Claims
Application Information

- R&D Engineer
- R&D Manager
- IP Professional
- Industry Leading Data Capabilities
- Powerful AI technology
- Patent DNA Extraction
Browse by: Latest US Patents, China's latest patents, Technical Efficacy Thesaurus, Application Domain, Technology Topic, Popular Technical Reports.
© 2024 PatSnap. All rights reserved.Legal|Privacy policy|Modern Slavery Act Transparency Statement|Sitemap|About US| Contact US: help@patsnap.com