An experimental platform for aero-engine vibration control
A technology of aero-engine and experimental platform, applied in the direction of engine test, vibration test, machine/structural component test, etc., can solve the problem of not being able to meet the further requirements, achieve less difficulty in transformation, avoid the failure of experimental results, and the cost of transformation low effect
- Summary
- Abstract
- Description
- Claims
- Application Information
AI Technical Summary
Problems solved by technology
Method used
Image
Examples
Embodiment 1
[0040] Example 1. Research on vibration characteristics of aero-engine high-pressure rotor:
[0041] Start the second drive motor 22, and the power output by the second drive motor 22 is transmitted to the high-voltage rotor through the output shaft and the transmission system near the aero-engine of the second coupling 7, thereby driving the rotation of the high-pressure rotor system 12 to simulate the high-pressure rotor of the aero-engine Operation; The capacitive displacement sensor 8 installed on the output shaft of the second drive motor 22 and the connecting shaft of the outer rotor of the aeroengine is used to measure the axial runout and radial runout of the rotating shaft. It is installed on the 2-3 level of the aeroengine The three-way acceleration sensor on box Ⅱ, 6-level receiver Ⅴ, combustion chamber receiver VI and high-pressure turbine receiver VII collects vibration acceleration signals, connects the sensor output line to the data acquisition system, and the data ...
Embodiment 2
[0042] Example 2: Research on vibration characteristics of aero-engine low-pressure rotor:
[0043] Start the first drive motor 21, the power output by the first drive motor 21 is transmitted to the low-pressure rotor system 11 through the output shaft and the first coupling 6, thereby driving the low-pressure rotor system 11 to rotate, simulating the operation of the low-pressure rotor of an aero engine, The working speed is 300r / min; the capacitive displacement sensor 8 installed on the connecting shaft between the output shaft of the first drive motor 21 and the inner rotor of the aero-engine is used to measure the axial and radial runout of the rotating shaft; it is installed on the aero-engine The three-way acceleration sensor on the 2-3 level receiver II, level 6 receiver V, combustion chamber receiver VI, and high-pressure turbine receiver VII corresponding to the 5 support bearings, collect vibration acceleration signals, and connect the sensor output line to data acquisit...
Embodiment 3
[0044] Example 3 Research on the vibration characteristics of the aero engine:
[0045] The first and second motors are started at the same time, and the two motors rotate forward synchronously to simulate the operation of the dual-rotor system of an aero-engine; the speed of the low-pressure rotor is 0~300r / min, and the speed of the high-pressure rotor is 0~1500r / min. A capacitive displacement sensor 8 on the output shaft of the drive motor 21, the inner rotor connecting shaft and the outer rotor connecting shaft of the aeroengine, used to measure the axial runout and radial runout of the rotating shaft; corresponding to the 5 support bearings installed in the aeroengine The three-way acceleration sensor on the 2-3-level receiver II, the sixth-level receiver V, the combustion chamber receiver VI and the high-pressure turbine receiver VII collects vibration acceleration signals; connect the sensor output line to the data acquisition system, and the data acquisition system will Af...
PUM
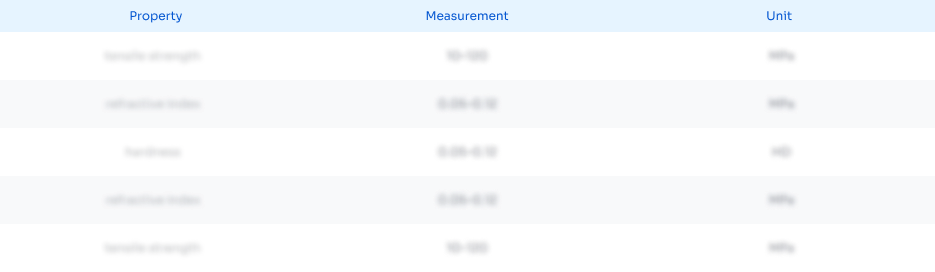
Abstract
Description
Claims
Application Information

- R&D Engineer
- R&D Manager
- IP Professional
- Industry Leading Data Capabilities
- Powerful AI technology
- Patent DNA Extraction
Browse by: Latest US Patents, China's latest patents, Technical Efficacy Thesaurus, Application Domain, Technology Topic, Popular Technical Reports.
© 2024 PatSnap. All rights reserved.Legal|Privacy policy|Modern Slavery Act Transparency Statement|Sitemap|About US| Contact US: help@patsnap.com