Vibration control experiment platform for aero-engine
An aero-engine and experimental platform technology, which is applied in the direction of engine testing, vibration testing, machine/structural component testing, etc., can solve problems such as not being able to meet further requirements, achieve low difficulty in transformation, avoid failure of experimental results, and improve the overall structure Scientific and reasonable effect
- Summary
- Abstract
- Description
- Claims
- Application Information
AI Technical Summary
Problems solved by technology
Method used
Image
Examples
Embodiment 1
[0040] Embodiment 1. Research on the vibration characteristics of high-pressure rotors of aero-engines:
[0041] Start the second driving motor 22, the power output by the second driving motor 22 is transmitted to the high-pressure rotor through the transmission system near the output shaft and the second coupling 7 aero-engine, thereby driving the rotation of the high-pressure rotor system 12, simulating the high-pressure rotor of the aero-engine Operation; by the capacitive displacement sensor 8 installed on the second drive motor 22 output shaft and the connecting shaft of the outer rotor of the aeroengine, it is used to measure the axial runout and radial runout of the rotating shaft. The three-way acceleration sensors on casing II, stage 6 casing V, combustion chamber casing VI and high-pressure turbine casing VII collect vibration acceleration signals, and connect the sensor output lines to the data acquisition system, which converts the collected signals into digital Af...
Embodiment 2
[0042] Embodiment 2. Research on the vibration characteristics of the low-pressure rotor of the aero-engine:
[0043] Start the first drive motor 21, the power output by the first drive motor 21 is transmitted to the low-pressure rotor system 11 through the output shaft and the first coupling 6, thereby driving the low-pressure rotor system 11 to rotate, simulating the operation of the low-pressure rotor of an aeroengine, and the low-pressure rotor The operating speed is 300r / min; the capacitive displacement sensor 8 installed on the output shaft of the first drive motor 21 and the connecting shaft of the inner rotor of the aeroengine is used to measure the axial runout and radial runout of the rotating shaft; The three-way acceleration sensors on the 2-3 stage casing II, the 6 stage casing V, the combustion chamber casing VI and the high-pressure turbine casing VII corresponding to the 5 support bearings collect vibration acceleration signals, and connect the sensor output lin...
Embodiment 3
[0044] Embodiment 3. Research on the vibration characteristics of the whole machine of the aero-engine:
[0045] Start the first and second motors at the same time, and the two motors rotate forward synchronously to simulate the operation of the dual-rotor system of the aero-engine; the speed of the low-pressure rotor is 0-300r / min, and the speed of the high-pressure rotor is 0-1500r / min A capacitive displacement sensor 8 on the output shaft of the driving motor 21, the connecting shaft of the inner rotor of the aeroengine and the connecting shaft of the outer rotor is used to measure the axial runout and radial runout of the rotating shaft; The three-way acceleration sensors on the 2-3 stage casing II, the 6 stage casing V, the combustion chamber casing VI and the high-pressure turbine casing VII collect vibration acceleration signals; connect the sensor output line to the data acquisition system, and the data acquisition system will After the collected signal is converted in...
PUM
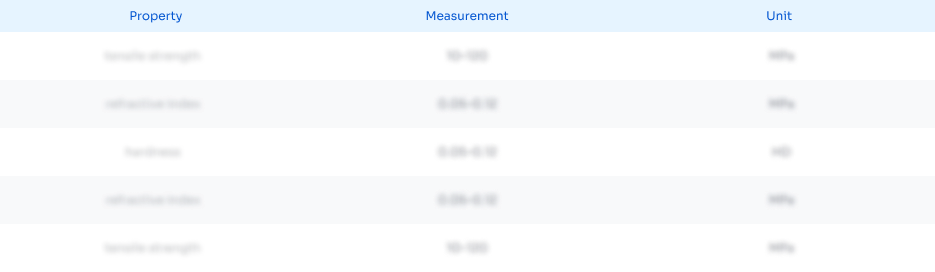
Abstract
Description
Claims
Application Information

- R&D
- Intellectual Property
- Life Sciences
- Materials
- Tech Scout
- Unparalleled Data Quality
- Higher Quality Content
- 60% Fewer Hallucinations
Browse by: Latest US Patents, China's latest patents, Technical Efficacy Thesaurus, Application Domain, Technology Topic, Popular Technical Reports.
© 2025 PatSnap. All rights reserved.Legal|Privacy policy|Modern Slavery Act Transparency Statement|Sitemap|About US| Contact US: help@patsnap.com