Novel anti-slippage process
A technology of anti-fraying and processing technology, applied in the field of weaving and sewing, can solve the problems of increased weaving cost, change of material feel, and inability to effectively solve problems such as cracks, so as to reduce the defective rate, enhance the fastness, and prevent yarn slippage. Effect
- Summary
- Abstract
- Description
- Claims
- Application Information
AI Technical Summary
Problems solved by technology
Method used
Image
Examples
Embodiment 1
[0036] Anti-slip treatment process, the method is as follows:
[0037] 1) Determine the seam
[0038] Reserve a seam of 1.2cm on the cut piece, overcoat the seam, and the stitch width of the overcoat line is 0.5cm.
[0039] 2) Net folding treatment of overcoat line
[0040] Fold the cover edge inward along the cover edge line, and press a 0.1cm wide open line along the folded part on the overlapped part to obtain a neatly folded cut piece.
[0041] 3) Flat seam stop
[0042] Face the two folded cut pieces face to face, and stitch them together at a distance of 0.6 cm from the above-mentioned folds with needle No. 11 of a lockstitch sewing machine. The stitch density of the stitched seams is 12 needles / 3 cm.
[0043] 4) Split seam
[0044] Take the patchwork pieces to the ironing table, and iron the patchwork into an open seam.
[0045] 5) Crimping
[0046] Use a No. 11 needle on a lockstitch sewing machine with a stitch density of 12 needles / 3cm to press open stitches wi...
Embodiment 2
[0048] Anti-slip treatment process, the method is as follows:
[0049] 1) Determine the seam
[0050] Reserve a seam of 1.2cm on the cut piece, overcoat the seam, and the stitch width of the overcoat line is 0.5cm.
[0051] 2) Net folding treatment of overcoat line
[0052] Fold the cover edge inward along the cover edge line, and press a 0.1cm wide open line along the folded part on the overlapped part to obtain a neatly folded cut piece.
[0053] 3) Flat seam stop
[0054] Face the two folded cut pieces face to face, and stitch them together at a distance of 0.6 cm from the above-mentioned folds with needle No. 11 of a lockstitch sewing machine. The stitch density of the stitched seams is 12 needles / 3 cm.
[0055] 4) Split seam
[0056] Take the patchwork pieces to the ironing table, and iron the patchwork into an open seam.
[0057] 5) Crimping
[0058] Use a No. 11 needle for a lockstitch sewing machine with a stitch density of 12 needles / 3cm. Along the slit, press o...
Embodiment 3
[0060] Anti-slip treatment process, the method is as follows:
[0061] 1) Determine the seam
[0062] Reserve a seam of 1.1cm on the cut piece, overcoat the seam, and the stitch width of the overcoat line is 0.45cm.
[0063] 2) Net folding treatment of overcoat line
[0064] Fold the cover edge inward along the cover edge line, and press a 0.1cm wide open line along the folded part on the overlapped part to obtain a neatly folded cut piece.
[0065] 3) Flat seam stop
[0066] Face the two folded pieces face to face, and stitch them together at a distance of 0.55 cm from the above-mentioned folds with needle No. 11 of a lockstitch sewing machine. The stitch density of the stitching is 14 needles / 3 cm.
[0067] 4) Split seam
[0068] Take the patchwork pieces to the ironing table, and iron the patchwork into an open seam.
[0069] 5) Crimping
[0070] Use a No. 11 needle on a lockstitch sewing machine with a stitch density of 14 stitches / 3cm to press open stitches with a w...
PUM
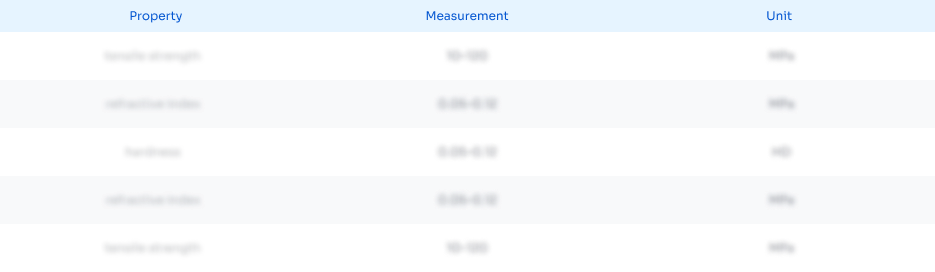
Abstract
Description
Claims
Application Information

- R&D
- Intellectual Property
- Life Sciences
- Materials
- Tech Scout
- Unparalleled Data Quality
- Higher Quality Content
- 60% Fewer Hallucinations
Browse by: Latest US Patents, China's latest patents, Technical Efficacy Thesaurus, Application Domain, Technology Topic, Popular Technical Reports.
© 2025 PatSnap. All rights reserved.Legal|Privacy policy|Modern Slavery Act Transparency Statement|Sitemap|About US| Contact US: help@patsnap.com