New submodel finite element analysis method based on cutting boundary deformation constraint
A boundary deformation, finite element technology, applied in special data processing applications, instruments, electrical digital data processing, etc., can solve problems such as sub-model stress distribution errors
- Summary
- Abstract
- Description
- Claims
- Application Information
AI Technical Summary
Problems solved by technology
Method used
Image
Examples
Embodiment Construction
[0084] Below in conjunction with accompanying drawing and specific embodiment the present invention is described in further detail:
[0085] A new method for submodel finite element analysis based on cutting boundary deformation constraints, image 3 Shown is a flow chart of a new method of sub-model finite element analysis based on cutting boundary deformation coupling of the present invention; the method includes the following steps:
[0086] Step 1: Establish a simplified model of the whole machine and analyze it
[0087] Use the APDL parametric modeling language in ANSYS software to establish a simplified finite element model of the whole machine through a bottom-up modeling method;
[0088] Step 2: Perform post-processing on the cutting boundary nodes of the whole machine model, and extract the resultant force component of the cutting boundary of the simplified model of the whole machine and the relative displacement of nodes. The extraction method includes the following...
PUM
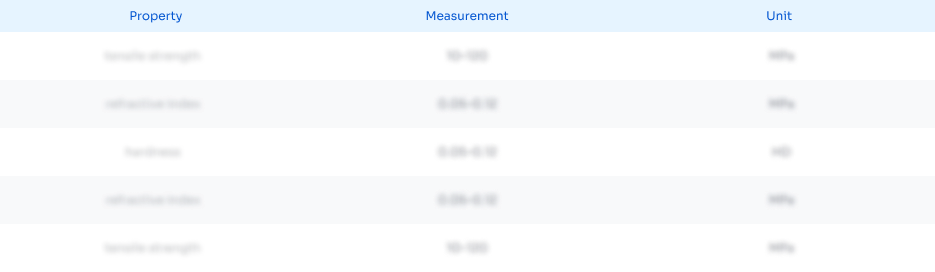
Abstract
Description
Claims
Application Information

- Generate Ideas
- Intellectual Property
- Life Sciences
- Materials
- Tech Scout
- Unparalleled Data Quality
- Higher Quality Content
- 60% Fewer Hallucinations
Browse by: Latest US Patents, China's latest patents, Technical Efficacy Thesaurus, Application Domain, Technology Topic, Popular Technical Reports.
© 2025 PatSnap. All rights reserved.Legal|Privacy policy|Modern Slavery Act Transparency Statement|Sitemap|About US| Contact US: help@patsnap.com