Prebaking aluminum cell anode set structure
An aluminum electrolytic cell and anode group technology, which is applied in the field of aluminum electrolytic anodes, can solve the problems of fluctuating working conditions of electrolytic cells, pollution, uneven conductivity of carbon electrodes, etc., and achieve the effects of fast and convenient connection process, tight connection, and cost reduction.
- Summary
- Abstract
- Description
- Claims
- Application Information
AI Technical Summary
Problems solved by technology
Method used
Image
Examples
Embodiment
[0026] Embodiment: a kind of prebaked aluminum electrolytic cell anode group structure, as attached Figure 1-2As shown, the mechanical steel claw bottom plate 9 is included, and the mechanical carbon block connection part is provided under the mechanical steel claw bottom plate 9, and the new anode carbon block 15 is connected to the bottom of the mechanical carbon block connection part, and the new anode carbon block 15 There is a T-shaped connection protrusion 19 on the upper part of the carbon block that is used in conjunction with the mechanical carbon block connection part. The T-shaped connection protrusion 19 on both sides of the upper part of the carbon block is provided with a T-shaped connection protrusion bearing shoulder 17. The bottom T-shaped connection groove 11 of the carbon block used in conjunction with the T-shaped connection protrusion 19 on the top of the carbon block is provided with a T-shaped connection groove hook bearing shoulder 18 at the bottom of t...
PUM
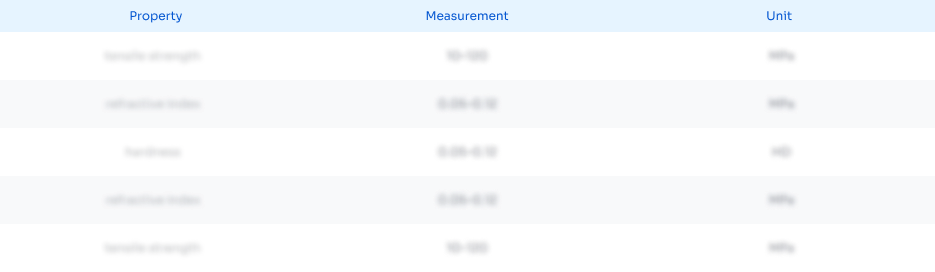
Abstract
Description
Claims
Application Information

- Generate Ideas
- Intellectual Property
- Life Sciences
- Materials
- Tech Scout
- Unparalleled Data Quality
- Higher Quality Content
- 60% Fewer Hallucinations
Browse by: Latest US Patents, China's latest patents, Technical Efficacy Thesaurus, Application Domain, Technology Topic, Popular Technical Reports.
© 2025 PatSnap. All rights reserved.Legal|Privacy policy|Modern Slavery Act Transparency Statement|Sitemap|About US| Contact US: help@patsnap.com