Open-loop control type manipulator
An open-loop control, robotic arm technology, applied in the field of robotic arms, can solve problems such as large displacement error, and achieve the effect of reducing displacement deviation
- Summary
- Abstract
- Description
- Claims
- Application Information
AI Technical Summary
Problems solved by technology
Method used
Image
Examples
Embodiment 1
[0030] figure 1 For the schematic diagram of the open-loop control mechanical arm provided by the embodiment of the present invention, please refer to figure 1 , the open-loop control type mechanical arm includes a frame 1 and a mechanical arm 2 movably mounted on the frame 1, the mechanical arm 2 is equipped with a first coil 3, and the frame 1 is equipped with The second coil 4, the first coil 3 and the second coil 4 are connected in parallel to the power supply circuit, the positions of the first coil 3 and the second coil 4 correspond to each other, and the transverse direction of the first coil 3 The cross section coincides with the cross section of the second coil 4 or is parallel to each other.
[0031] When in use, after the automatic reset of the mechanical arm 2 ends, within the time interval between the reset termination of the mechanical arm 2 and the start of the next cycle, the direction of the first coil 3 and the second coil 4 are simultaneously passed to In ...
Embodiment 2
[0035] figure 1 For the schematic diagram of the open-loop control mechanical arm provided by the embodiment of the present invention, please refer to figure 1 , the open-loop control type mechanical arm includes a frame 1 and a mechanical arm 2 movably mounted on the frame 1, the mechanical arm 2 is equipped with a first coil 3, and the frame 1 is equipped with The second coil 4, the first coil 3 and the second coil 4 are connected in parallel to the power supply circuit, the positions of the first coil 3 and the second coil 4 correspond to each other, and the transverse direction of the first coil 3 The cross section coincides with the cross section of the second coil 4 or is parallel to each other.
[0036]When in use, after the automatic reset of the mechanical arm 2 ends, within the time interval between the reset termination of the mechanical arm 2 and the start of the next cycle, the direction of the first coil 3 and the second coil 4 are simultaneously passed to In t...
PUM
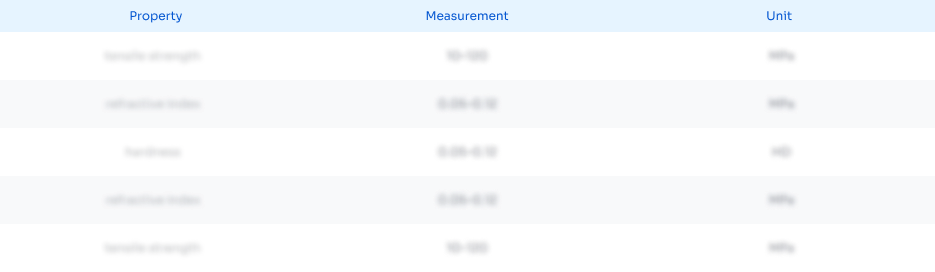
Abstract
Description
Claims
Application Information

- Generate Ideas
- Intellectual Property
- Life Sciences
- Materials
- Tech Scout
- Unparalleled Data Quality
- Higher Quality Content
- 60% Fewer Hallucinations
Browse by: Latest US Patents, China's latest patents, Technical Efficacy Thesaurus, Application Domain, Technology Topic, Popular Technical Reports.
© 2025 PatSnap. All rights reserved.Legal|Privacy policy|Modern Slavery Act Transparency Statement|Sitemap|About US| Contact US: help@patsnap.com