Multifunctional numerical-control spherical optical element milling and grinding tool
A technology of spherical optics and optical elements, applied in optical elements, optical surface grinders, optics, etc., can solve problems such as unfavorable small batch and multi-variety processing, and achieve the effect of improving processing efficiency and reducing the link of tooling adjustment
- Summary
- Abstract
- Description
- Claims
- Application Information
AI Technical Summary
Problems solved by technology
Method used
Image
Examples
Embodiment Construction
[0018] In order to make the purpose, content and advantages of the present invention clearer, the specific implementation manners of the present invention will be further described in detail below in conjunction with the accompanying drawings and embodiments.
[0019] refer to figure 1 As shown, the multifunctional spherical optical element CNC milling tooling of this embodiment includes a fixture body 1, a water storage tank 2, a connecting screw 3 and a connecting head 4.
[0020] Fixture main body 1 is made of bakelite material, comprises body, the concave spherical surface formed on the upper part of the body, the annular platform formed on the periphery of the concave spherical surface, and the annular convex spherical surface formed on the periphery of the annular platform; the radius of the concave spherical surface is the same as that to be The radius of the convex surface of the processed optical element is the same, which is used to support the convex surface of the ...
PUM
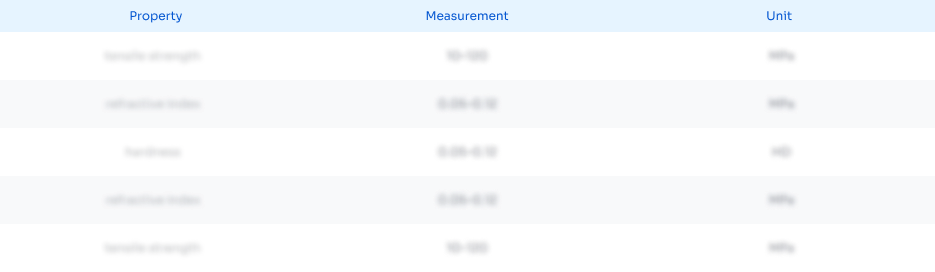
Abstract
Description
Claims
Application Information

- Generate Ideas
- Intellectual Property
- Life Sciences
- Materials
- Tech Scout
- Unparalleled Data Quality
- Higher Quality Content
- 60% Fewer Hallucinations
Browse by: Latest US Patents, China's latest patents, Technical Efficacy Thesaurus, Application Domain, Technology Topic, Popular Technical Reports.
© 2025 PatSnap. All rights reserved.Legal|Privacy policy|Modern Slavery Act Transparency Statement|Sitemap|About US| Contact US: help@patsnap.com