Deep hole processing method adopting common lathe
A processing method and technology of ordinary lathes, which are applied in the field of deep hole processing of ordinary lathes, can solve problems such as difficulty in meeting requirements, small dimensional accuracy and small surface roughness values, and achieve the effects of reducing production costs, simplifying the processing process, and satisfying the processing accuracy.
- Summary
- Abstract
- Description
- Claims
- Application Information
AI Technical Summary
Problems solved by technology
Method used
Examples
Embodiment Construction
[0017] Common lathe deep hole processing method of the present invention comprises the following steps:
[0018] The first step is to leave a machining allowance of 1mm for the total length of both ends of the car, and chamfer 2×30° at both ends of the hole, and use two tops to clamp the outer circle of the rough car to leave a margin of 0.5mm on one side;
[0019] In the second step, one end of the workpiece is clamped, and the other end is supported by a center frame. Use an inner hole cutter to rough half the total length of the inner hole, leaving a margin of 0.5mm on one side;
[0020] In the third step, the workpiece is turned around, and the remaining hole length is left at the other end of the rough car, leaving a margin of 0.5mm on one side of the inner hole;
[0021] The fourth step is to finish the two ends of the car and control the total length of the workpiece, and the chamfering of the holes at both ends is 2×30°;
[0022] The fifth step is to use two thimbles ...
PUM
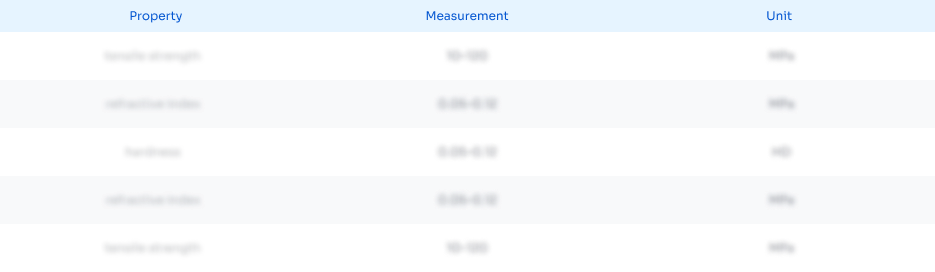
Abstract
Description
Claims
Application Information

- Generate Ideas
- Intellectual Property
- Life Sciences
- Materials
- Tech Scout
- Unparalleled Data Quality
- Higher Quality Content
- 60% Fewer Hallucinations
Browse by: Latest US Patents, China's latest patents, Technical Efficacy Thesaurus, Application Domain, Technology Topic, Popular Technical Reports.
© 2025 PatSnap. All rights reserved.Legal|Privacy policy|Modern Slavery Act Transparency Statement|Sitemap|About US| Contact US: help@patsnap.com